The Rise of the Digital Thread: Eliminating Data Silos in Manufacturing
In an era where efficiency and agility are more crucial than ever, a digital thread is no longer just an advantage — it’s a necessity. The post The Rise of the Digital Thread: Eliminating Data Silos in Manufacturing appeared first on Fabricating & Metalworking.

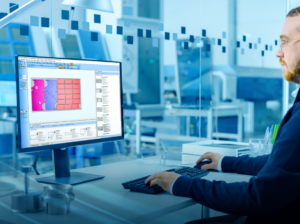
For today’s manufacturers, integrating new tools, technologies, and processes into existing systems can feel like a huge undertaking. Over time, companies accumulate an array of software and hardware across the manufacturing lifecycle, each performing a specific function but often operating in a silo. With only 2% of manufacturers claiming to be problem-free with their data practices, fragmentation and lack of connected data results in data gaps, inefficiencies, and sometimes costly errors for most manufacturers. Creating a single digital thread by enabling a single flow of data that connects the entire manufacturing process is a powerful emerging solution to streamline operations, improve data flow, and ultimately increase competitiveness. While spanning quoting, design and engineering, manufacturing and distribution is a tall order, digital threads are becoming an essential strategy for manufacturers.
Challenges in Integrating Processes and Systems
Because a company’s various tools are rarely designed to work together seamlessly, especially across different stages of the production lifecycle, the integration of disparate technologies poses one of the biggest challenges. For instance, quoting, design, manufacturing, and distribution teams may each use their own specialized systems, which can complicate the flow of information. When data from quoting doesn’t pass automatically into manufacturing, or if distribution lacks real-time production insights, inefficiencies, and communication breakdowns are inevitable.
Manufacturers also struggle to ensure that legacy systems are compatible with modern digital platforms. And it’s not only a technology integration problem. The “we’ve always done it this way” mentality can also create barriers to creating a digital thread. In some cases, it’s not just about upgrading equipment; it’s about changing the organizational culture and training teams to better leverage data.
The Growing Demand for Digital Threads

Unlike traditional systems, a digital thread can link each stage of production, from initial quoting to design adjustments, manufacturing processes like nesting, and final distribution. This single-thread approach allows manufacturers to pull data directly into systems where it’s needed, reducing the time spent on manual data handling and improving real-time visibility across departments.
Since the majority of manufacturing business leaders realize that better collaboration can improve product quality (88%) and time to market (86%), the demand for integrated digital systems is growing as companies look to remain competitive in an evolving market. Manufacturers are scrutinizing every aspect of their workflows to find cost savings, speed up delivery and reduce errors. However, many overlook the time and resources required to manage data flows across departments. For instance, companies may spend significant time re-entering data into multiple systems increasing the risk of lost or incomplete information and delaying progress, but with connected data, they eliminate this risk.
Benefits of a Digital Thread for Various Stakeholders
The digital thread offers distinct advantages to everyone involved in metalworking, from quoting teams to shop floor operators and distribution managers. For quoting teams, an integrated system provides immediate access to accurate design data, allowing for more precise pricing and faster response times. Design and engineering teams can collaborate with manufacturing, using tools like digital twins to prototype virtually and assess whether parts can be manufactured as a single unit, eliminating the need for additional fixturing or welding.
For operators on the shop floor, integrating data from quoting and design enables better programming of equipment. Real-time data flow ensures that operators have accurate flat patterns, avoiding scrap and costly rework. Distribution teams also benefit from a digital thread, as they receive up-to-date information on production schedules, allowing them to plan logistics more effectively.
A good example of how integration can improve efficiency is with nesting software, which enables combined jobs to maximize material utilization. Traditionally, a programmer would receive a list of jobs and then manually determine how to nest parts to maximize material usage while considering operational constraints. With a digital thread, nesting software can pull job data directly from design and manufacturing systems, automatically identifying parts that can be merged into a single layout to minimize material waste. This not only speeds up the nesting process but also reduces the risk of errors since data flows automatically rather than being entered manually. Additionally, this approach keeps welding and other downstream processes on schedule, as production bottlenecks are minimized.
Approach to Implementing a Digital Thread
Implementing a digital thread is a journey, not a one-time setup. Companies should begin by assessing their current systems and understanding where they need to go. This involves evaluating the types of products they’re making and identifying the biggest pain points that digital integration and better data sharing could resolve. A strategic implementation plan that prioritizes the highest-impact changes first can help sustain momentum and demonstrate value quickly.
Manufacturers should also consider tools designed to facilitate integration. Software that connects different design systems can help retain vital digital information and pass it seamlessly into downstream applications. Scheduling tools enable manufacturers to pull in a laser-cutting schedule, streamlining shop floor operations. Implementing these tools help foster a culture that embraces digital transformation — empowering the workforce to make data-backed decisions will attract younger workers who are used to having data at their fingertips.
The Future of Digital Threads in Manufacturing
The digital thread is still evolving, and its future will likely involve even more sophisticated technologies. With the right data flowing in, emerging tools like AI and machine learning can analyze machine performance over time to optimize settings, potentially replacing operator judgment with data-driven insights. These advancements could make digital threads even more valuable, further reducing downtime and enabling predictive maintenance.
As the manufacturing industry advances, companies that adopt a comprehensive digital thread approach will be better positioned to compete. By integrating quoting, design, manufacturing, and distribution into a single cohesive system, they can reduce waste, accelerate production, and adapt to changing demands more effectively. In an era where efficiency and agility are more crucial than ever, a digital thread is no longer just an advantage — it’s a necessity.
The post The Rise of the Digital Thread: Eliminating Data Silos in Manufacturing appeared first on Fabricating & Metalworking.