Job-hit automotive suppliers brace for a very different future
GKN's last UK automotive parts plant closed in 2021 Headwinds including electrification and China are forcing a number of prominent suppliers to restructure The once-in-a-generation upheaval currently sending shockwaves through Europe’s suppliers has multiple consequences, one of which has been to close the book on a key part of British automotive history. Back in January, Dowlais, the parent company of driveshaft specialist GKN Automotive, was sold to American Axle. “This whole sector has been really challenged over the last 18-24 months,” Dowlais CEO Liam Butterworth told Autocar, and selling up will allow the company to “to navigate this structural shift in the industry". GKN can trace its history back to 1759, when the Dowlais Ironworks Co was established in South Wales. What became Guest, Keen & Nettlefolds and then GKN has reinvented itself multiple times over the centuries, but this last move takes ownership out of British hands for the first time. “The overall macro in the industry is changing,” Butterworth said on the company’s earnings call on 5 March. “There's a structural change taking place around tariffs, geopolitics, regionalisation, the different requirements from our customers and thus creating a strong headwind for a number of automotive suppliers.” Last year, European automotive suppliers announced 54,000 job cuts – more than in the Covid years of 2020 and 2021 put together, according to data from the European Association of Automotive Suppliers (Clepa). Among those numbers are 5550 at Germany’s Bosch, the largest automotive supplier, according to Automotive News's 2024 top 100 parts suppliers list. Number two on that list, ZF Friedrichshafen, announced it would axe 12,000 jobs in Germany. Meanwhile, Continental is looking to lose 7150 jobs through global restructuring, while Schaeffler has said it wants to cut 4700 across Europe, 2800 of those in Germany. Germany’s role as the region’s car-building heartland has meant many of the world’s global tier-one super-suppliers growing to vast sizes within its borders, so the country is being disproportionally affected as the pressures of electrification, China and a shrinking car market force restructuring. Almost 19,000 automotive jobs (including at car companies) were lost last year within Germany, according to research from consultantcy EY. “The German automotive industry is in a massive and comprehensive crisis," EY automotive expert Constantin Gall said. “There has been a massive tightening of the cost screw". In the UK, the sale of GKN is the biggest evidence of that upheaval to hit the supply industry, but there are job losses too. GKN’s last UK automotive parts plant shut in 2021 and Butterworth said in March that the company would also shut its electric powertrain research centre, established in 2017. Meanwhile, new GKN owner American Axle shut its Albion Automotive facility in Glasgow in October and Schaeffler announced in November that it would shut its clutch factory in near Sheffield, citing a reduced demand for clutches globally. The multi-billion pound parts industry was always going to vulnerable to an industry-wide forensic focus on costs, given their outsize contribution to the average cost of building a car. “The total cost of an automobile is 85% parts, 10% the plant and 5% logistics,” former Stellantis CEO and rigorous bill-slasher Carlos Tavares said last year. “The double digits in sourcing reduction [costs] are going to come from the 85%. The guy that reaches that first will be the winner.” Tesla CEO Elon Musk has in the past derided the legacy car business as “catalogue engineering” for its reliance on supplier giants like Bosch, Continental and others. The shift to electrification has prompted car companies to promise root-and-branch changes to the way they engineer and build cars, to the detriment of the size of the pie given to suppliers. For example, Renault under Luca de Meo has promised to slash the number of parts in future models like the Twingo EV from around 2500 per vehicle to 1100. Car makers are keen to soften some of their own job-reduction requirements by bringing in-house parts that previously might have been outsourced to suppliers. Electric drive units containing the motor, invertor and transmission are a good example – for example Ford in Halewood and JLR in Wolverhampton. That cuts the available pool of customers for suppliers. “We've had a number of cases where we've walked away from some contracts because it just doesn't make commercial sense,” GKN’s Butterworth said. “If somebody else wants to pick up a contract that's loss-making, then good luck to them.” When they do land a decent contract, suppliers are at risk from erroneous volume predictions, especially those made during the optimism of EV growth three or four years ago. GKN said its 2024 revenue on the e-drive front was hit by volume decline in four specific model programmes, of which Butterworth singled out the Fiat 500e. “Basicall
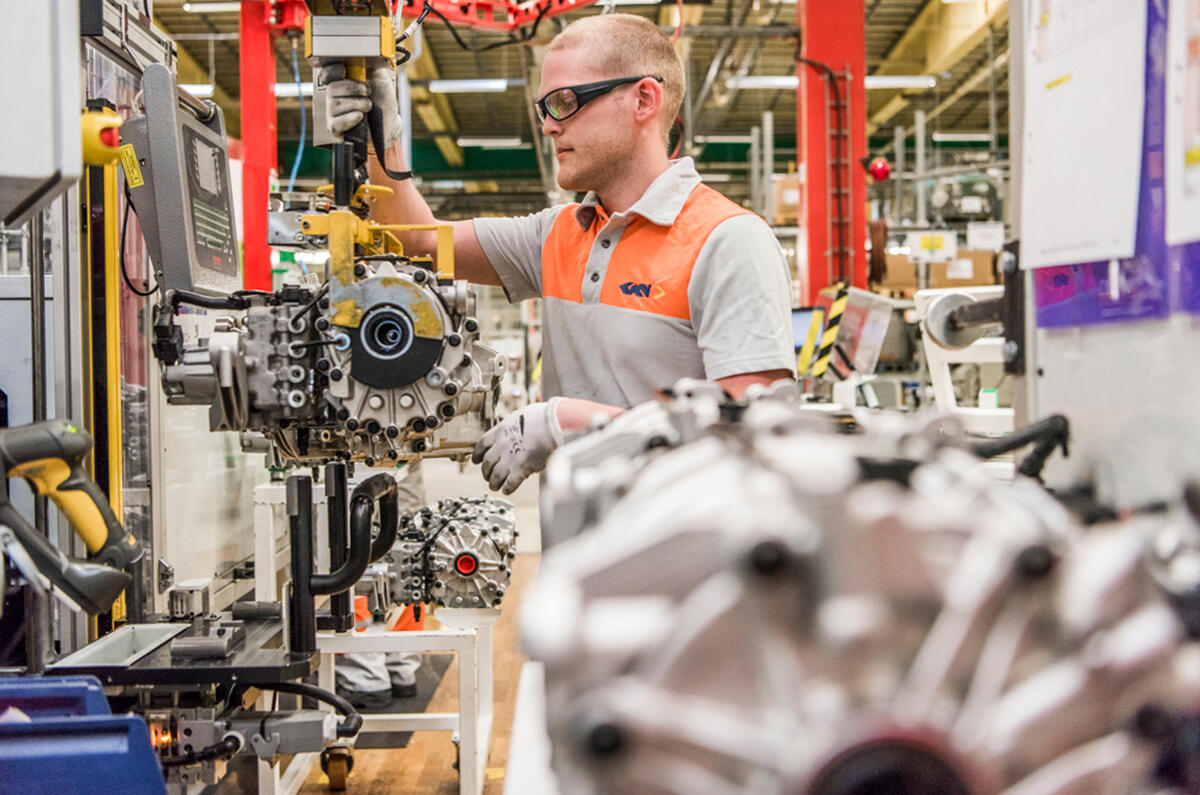
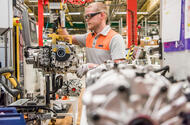
GKN's last UK automotive parts plant closed in 2021Headwinds including electrification and China are forcing a number of prominent suppliers to restructure
The once-in-a-generation upheaval currently sending shockwaves through Europe’s suppliers has multiple consequences, one of which has been to close the book on a key part of British automotive history.
Back in January, Dowlais, the parent company of driveshaft specialist GKN Automotive, was sold to American Axle. “This whole sector has been really challenged over the last 18-24 months,” Dowlais CEO Liam Butterworth told Autocar, and selling up will allow the company to “to navigate this structural shift in the industry".
GKN can trace its history back to 1759, when the Dowlais Ironworks Co was established in South Wales. What became Guest, Keen & Nettlefolds and then GKN has reinvented itself multiple times over the centuries, but this last move takes ownership out of British hands for the first time.
“The overall macro in the industry is changing,” Butterworth said on the company’s earnings call on 5 March. “There's a structural change taking place around tariffs, geopolitics, regionalisation, the different requirements from our customers and thus creating a strong headwind for a number of automotive suppliers.”
Last year, European automotive suppliers announced 54,000 job cuts – more than in the Covid years of 2020 and 2021 put together, according to data from the European Association of Automotive Suppliers (Clepa).
Among those numbers are 5550 at Germany’s Bosch, the largest automotive supplier, according to Automotive News's 2024 top 100 parts suppliers list.
Number two on that list, ZF Friedrichshafen, announced it would axe 12,000 jobs in Germany. Meanwhile, Continental is looking to lose 7150 jobs through global restructuring, while Schaeffler has said it wants to cut 4700 across Europe, 2800 of those in Germany.
Germany’s role as the region’s car-building heartland has meant many of the world’s global tier-one super-suppliers growing to vast sizes within its borders, so the country is being disproportionally affected as the pressures of electrification, China and a shrinking car market force restructuring.
Almost 19,000 automotive jobs (including at car companies) were lost last year within Germany, according to research from consultantcy EY. “The German automotive industry is in a massive and comprehensive crisis," EY automotive expert Constantin Gall said. “There has been a massive tightening of the cost screw".
In the UK, the sale of GKN is the biggest evidence of that upheaval to hit the supply industry, but there are job losses too. GKN’s last UK automotive parts plant shut in 2021 and Butterworth said in March that the company would also shut its electric powertrain research centre, established in 2017.
Meanwhile, new GKN owner American Axle shut its Albion Automotive facility in Glasgow in October and Schaeffler announced in November that it would shut its clutch factory in near Sheffield, citing a reduced demand for clutches globally.
The multi-billion pound parts industry was always going to vulnerable to an industry-wide forensic focus on costs, given their outsize contribution to the average cost of building a car.
“The total cost of an automobile is 85% parts, 10% the plant and 5% logistics,” former Stellantis CEO and rigorous bill-slasher Carlos Tavares said last year. “The double digits in sourcing reduction [costs] are going to come from the 85%. The guy that reaches that first will be the winner.”
Tesla CEO Elon Musk has in the past derided the legacy car business as “catalogue engineering” for its reliance on supplier giants like Bosch, Continental and others.
The shift to electrification has prompted car companies to promise root-and-branch changes to the way they engineer and build cars, to the detriment of the size of the pie given to suppliers.
For example, Renault under Luca de Meo has promised to slash the number of parts in future models like the Twingo EV from around 2500 per vehicle to 1100.
Car makers are keen to soften some of their own job-reduction requirements by bringing in-house parts that previously might have been outsourced to suppliers.
Electric drive units containing the motor, invertor and transmission are a good example – for example Ford in Halewood and JLR in Wolverhampton.
That cuts the available pool of customers for suppliers. “We've had a number of cases where we've walked away from some contracts because it just doesn't make commercial sense,” GKN’s Butterworth said. “If somebody else wants to pick up a contract that's loss-making, then good luck to them.”
When they do land a decent contract, suppliers are at risk from erroneous volume predictions, especially those made during the optimism of EV growth three or four years ago.
GKN said its 2024 revenue on the e-drive front was hit by volume decline in four specific model programmes, of which Butterworth singled out the Fiat 500e. “Basically the volumes fell off a cliff in Q1 last year when all of the incentives were stopped, specifically in Germany and Italy, and that dried up demand for that vehicle,” he said.
The sizeable bill to moving to electric is painful but has to be paid, given the gulf in production costs between Europe and China and the danger posed by competition from that direction. “The pressure is probably higher than it's been than I've seen it for quite some time,” Butterworth said.
Much of that burden is being passed onto suppliers, forcing them to make difficult decisions. “That can't come from just reducing prices; it needs to come from taking costs out of the system," said Butterworth. "From smarter material purchasing, lower cost manufacturing footprint and more VAVE [value analysis, value engineering] and looking at smarter cleverer ways of engineering and designing things."
Moving manufacturing to lower-cost eastern Europe or further afield is a favourite cost-cutting method. GKN, for example, moved its Birmingham driveshaft production to Poland. Schaeffler said passenger car clutches made in Sheffield would go to Hungary, while those for tractors will move to India.
Many suppliers are restructuring. For example, Continental will spin off its automotive division in September. “We are fully convinced that companies being focused and fast have a clear advantage in this tough industry environment,” CEO Nikolai Setzer said on a special call to investors in March. “The last years, and in particular right now, are as dynamic as they have ever been.”
Clepa is hoping the European Union will help by slowing down the timeline to move to electric and allow car makers to carry on building technologies with a higher part count. “The EU must embrace a diverse portfolio of sustainable technologies, including plug-in hybrids, range-extenders, hydrogen and renewable fuels,” the lobby group said in a statement that otherwise broadly welcomed the EU's recently proposed automotive Action Plan.
In a recent survey of Clepa members, 42% of respondents said they expected a loss or close to zero profit this year. As Peter Bryntesson, CEO of the Scandinavian automotive parts association FKG, told the Dagens Industri newspaper: "Spring 2025 looks pitch black."