Combat engineering evolves with autonomy and robotics
[Sponsored] Robotic combat engineering will reduce risk to soldiers in the breach while maintaining or increasing the tempo of movement for maneuver forces.
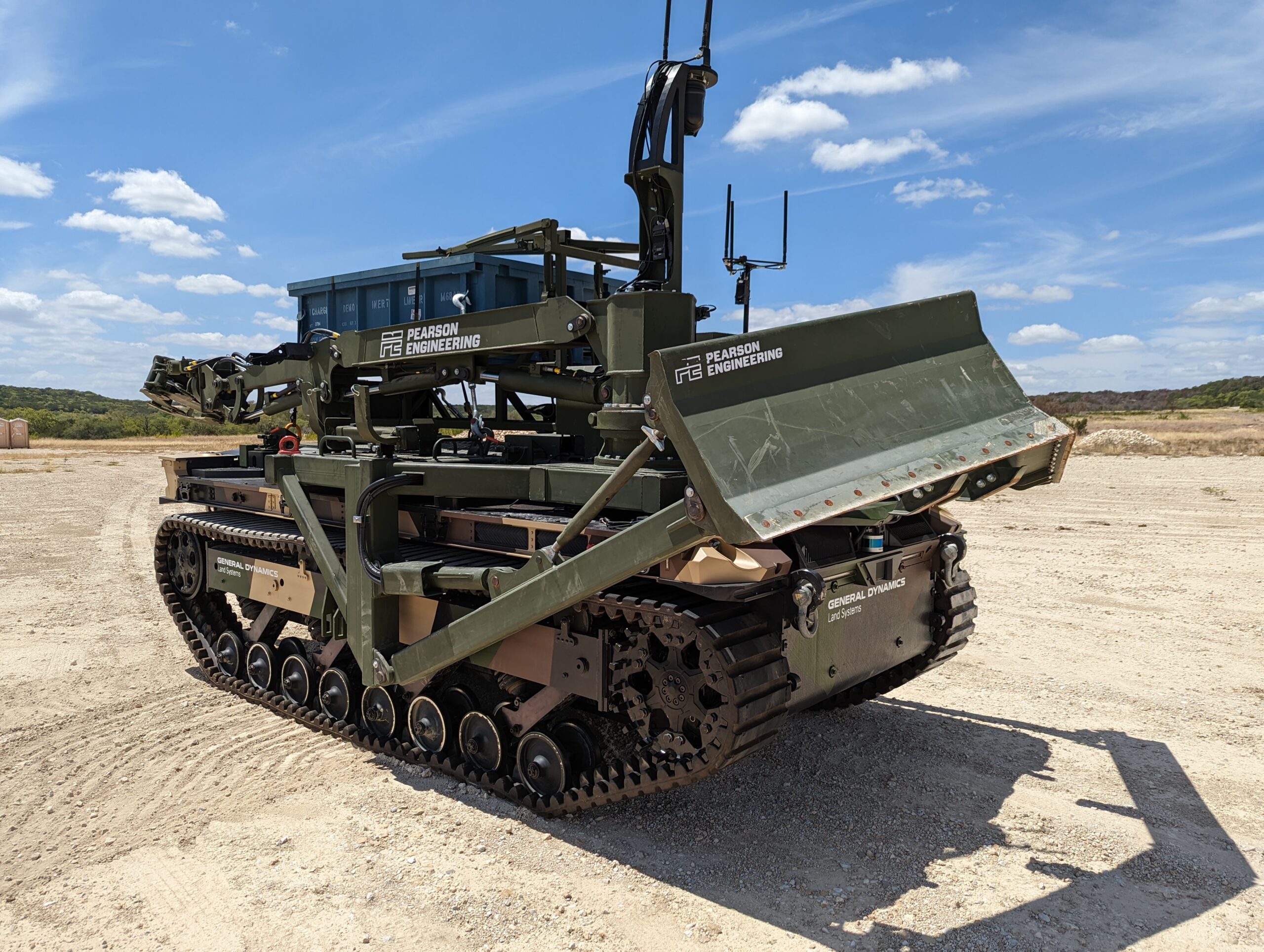
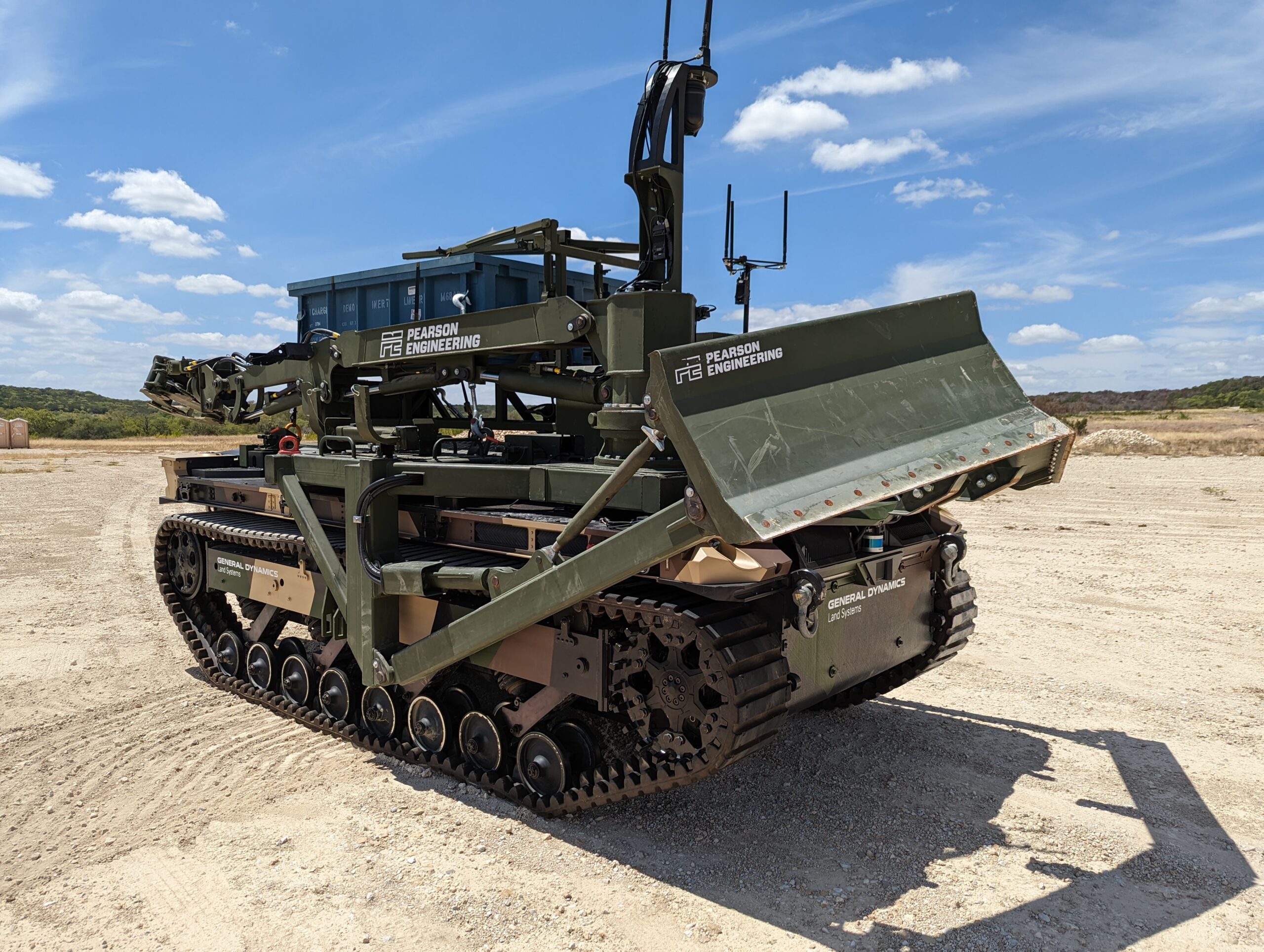
(Pearson Engineering photo).
Pearson Engineering’s latest developments include solutions that incorporate tele-operation, automation, and autonomy for front-end equipment and engineering mission packs designed specifically for robotic platforms. We discuss autonomous combat engineering with Amish Patel, senior engineer for robotics solutions at Pearson Engineering.
Pearson Engineering focuses on the medium tier of RCVs that are in a weight class suitable for combat engineering roles. Which RCVs are we talking about, to execute what combat engineering tasks? What are the combat engineering challenges for this tier of robot?
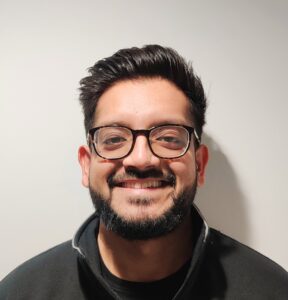
Amish Patel is senior engineer, Robotic Solutions Engineering, Pearson Engineering.
The medium tier of RCVs, or the RCV-M variant tier, per the U.S. DoD’s classification, encompasses robotic vehicles that fall within the 10-20 ton weight category. Having a greater vehicle mass is favoured for combat engineering tasks requiring ground engaging front-end equipment.
The medium tier of RCV’s is lighter than traditional armoured engineering vehicles. Ground engaging combat engineering equipment for use with these RCV’s will need to be designed to fully utilise the available tractive effort from the host RCV.
Example combat engineering tasks could include route proving and clearance, gap crossing, minefield breaching and urban obstacle creation and reduction.
Tell us about your enabling technologies and solutions for these robotic platforms – the front-end equipment and tools that help the Army complete a task.
Our latest developments include solutions that incorporate tele-operation, automation and autonomous capabilities to front-end equipment and engineering tools designed specifically for robotic platforms. Such developments have been designed to be modular and scalable, allowing them to be mounted onto RCV-Ms from multiple OEMs.
Through the use of integrated sensor technologies and digital tools, augmented operator aids can be implemented to simplify tele-operation of front-end equipment and engineering tools. For example, graphical overlays can be used to aid depth perception when teleoperating manipulator arms, increasing operational tempo and reducing mission completion times.
Integration with battlefield management systems
BMS systems could provide the networking backbone to enable autonomous control of multiple RCV platforms to simultaneously complete combat engineering tasks and missions at pace. Other sensor payloads integrated in the same BMS could also provide RCVs with increased situational awareness to execute tasks with greater precision and momentum.
Describe your RCV-Pioneer concept, which involves developing modular, swappable payloads for RCV platforms rather than building the vehicles themselves. How does this capability reduce the time it takes to reduce an obstacle or breach a minefield?
RCV-Pioneer provides uncrewed ground vehicles with robotic engineering capability, paving the way for modern combat engineering CONOPS. Leveraging the power of mature artificial intelligence and autonomy will allow for robotic engineering assets to work together as a force multiplier, increasing survivability and freedom of movement.
Such technologies will enable UGVs to rapidly interchange modular mission payloads in a matter of minutes, providing vast flexibility for dynamic mission profiles. This increase in the quantity and diversity of robotic combat engineering units in warfare will enable simultaneous execution of engineering operations across the battlefield, creating an unprecedented pace of advancement for friendly forces to counter the adversary with minimal risk to personnel.
The use of autonomous systems will allow for advanced analysis of the mission profile, including the ability to rapidly simulate outcomes with a given RCV and MMP combination when applied in different ways. The optimal set of steps to reduce the obstacle or breach a minefield can then be identified and the RCV and MMP subsequently deployed to execute at pace.
Describe your views on the need for CONOPS around the employment of autonomous engineering vehicles for combat engineering.
Employing robotic engineering vehicles will require a new set of CONOPS to be developed to fully utilise the benefits that robotic platforms can provide. For example, robotic assets could be deployed in an autonomous manner to jointly undertake combat engineering tasks, however a human-in-the-loop may still be required to tele-operate platforms when faced with a scenario that the autonomous system cannot overcome.
The C2 networking backbone would also need to be optimised to account for the bandwidth of all robotic assets that are deployed; integrated autonomy would inherently reduce this burden. CONOPS will need to factor in a means by which the humans operating in partnership with the autonomous engineering vehicles are able to understand how the vehicles are executing the mission. This will be important to build operator trust in autonomous systems and limit unnecessary intervention that may hinder progress. CONOPS will need to take account of how the autonomous engineering vehicle behaves if comms to the command centre are lost or the platform is immobilised, temporarily or permanently.
What is your perspective on the potential for upgrading existing crewed engineering vehicles to provide autonomous capabilities, such as the M1150 Assault Breacher Vehicle?
Pearson Engineering has successfully developed and tested tele-operation kits which can be retrofitted onto existing engineering vehicles, such as the M1150 ABV. One of the main capabilities of the system is that the vehicle can be switched between remote and manual control at the flick of a switch, allowing for fast changeover when used for dynamic mission profiles.
Our retrofittable tele-operation kits reduce the burden of operator training through familiarity of existing platforms and provide a safe path to deploy teleoperated assets and remove soldiers from harm’s way sooner. Retrofitting existing crewed engineering vehicles to provide teleoperated or autonomous combat engineering capabilities could be a cost-effective alternative to developing robotic platforms from the ground up. It is an approach that enables combat engineering tasks to be automated and soldiers removed from harm’s way in the nearer term, ahead of advanced RCV’s coming into service.
Final thoughts?
As technology advances and ground vehicles evolve, we are keeping pace by offering a modern approach to engineering capability in what is quickly becoming a remote and autonomous world.
The development of RCV-Pioneer follows the core principles of Pearson Engineering’s approach, providing high levels of equipment flexibility to support mission adaptability.
Whilst best known for providing a suite of tools for vehicles such as the Assault Breacher Vehicle, Pearson Engineering’s investment in research and development is seeing us deliver a new generation of capability that will ultimately take soldiers away from the most hazardous tasks.