Beyond Resilience: 5 Steps to Building an Antifragile Supply Chain
Why Resilience Is No Longer Enough Supply chains were once designed for efficiency, not disruption. But in today’s world of pandemics, geopolitical shocks, and extreme weather events, efficiency alone is a fragile strategy. The goal is no longer just resilience – it’s antifragility. Coined by Nassim Taleb, antifragility means getting stronger from shocks, rather than […] The post Beyond Resilience: 5 Steps to Building an Antifragile Supply Chain appeared first on Logistics Viewpoints.
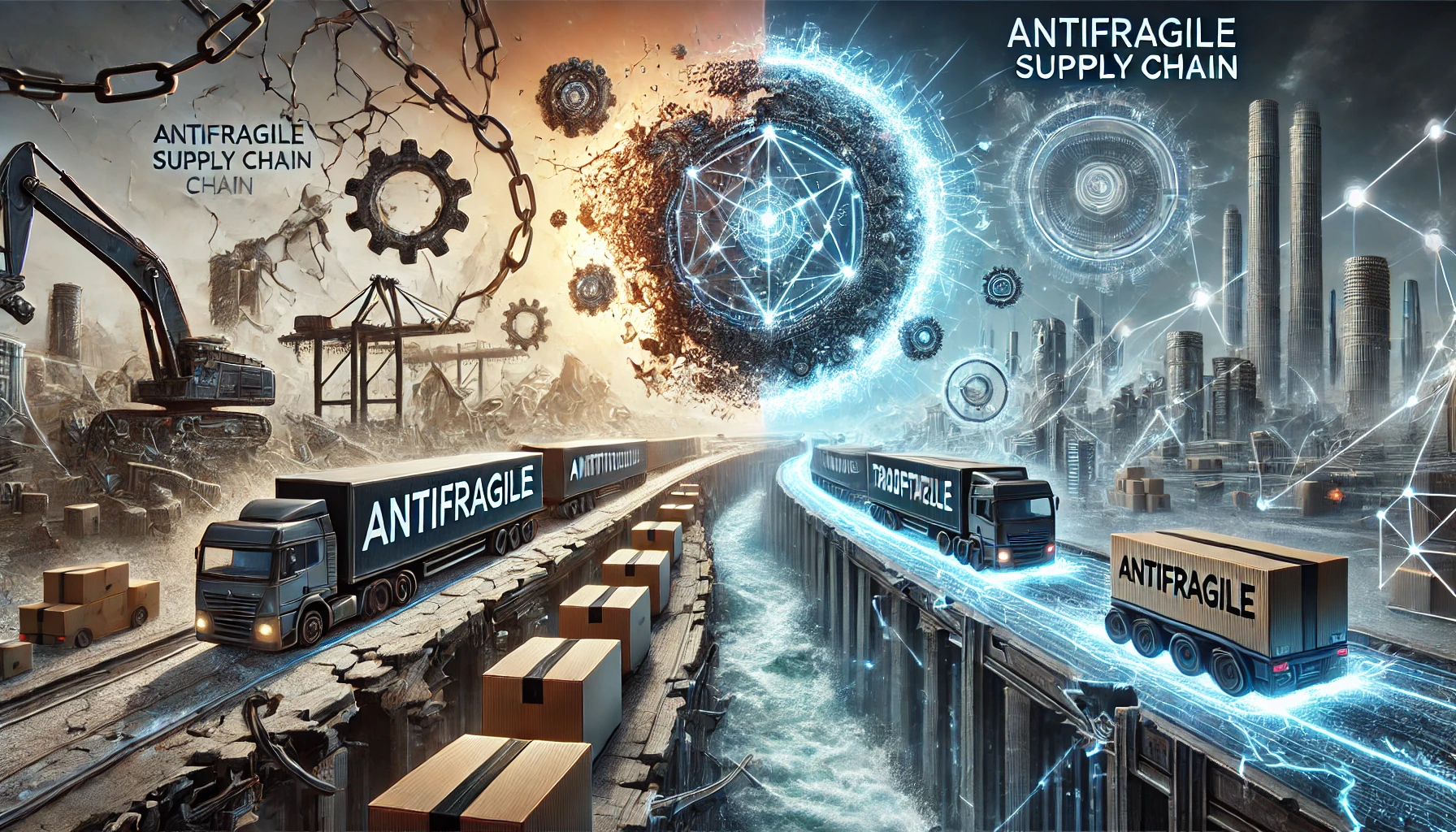
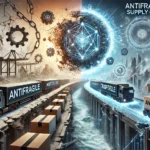
Why Resilience Is No Longer Enough
Supply chains were once designed for efficiency, not disruption. But in today’s world of pandemics, geopolitical shocks, and extreme weather events, efficiency alone is a fragile strategy.
The goal is no longer just resilience – it’s antifragility.
Coined by Nassim Taleb, antifragility means getting stronger from shocks, rather than just surviving them. The best supply chains don’t just withstand disruptions – they thrive in uncertainty, using crises as catalysts for improvement.
But how do you engineer antifragility into your supply chain?
This guide provides a 5-step framework, blending proven resilience models (Simchi-Levi’s TTR-TTS, Sheffi’s strategy, the Kraljic Matrix, network science, and OODA Loop) to create a supply chain that not only survives disruptions but becomes stronger from them.
Step 1: Identify Breaking Points in Your Supply Chain
Before fixing your supply chain, you need to know where it breaks under pressure. The TTR-TTS framework, developed by Simchi-Levi, provides a structured way to identify vulnerabilities.
TTR-TTS Framework
TTR (Time-to-Recover) represents the time needed to restore supply after a disruption, while TTS (Time-to-Survive) is the duration a company can continue operations before running out of inventory. When TTR exceeds TTS, a weak link is exposed in the supply chain.
Action Plan:
- Map your supply chain, visualizing key nodes (suppliers, plants, logistics hubs).
- Calculate TTR and TTS for each node and subtract (TTR – TTS).
- If TTR > TTS, that node is at risk and requires a contingency plan.
Step 2: Prioritize Supplier Risks Using the Kraljic Matrix
Not all suppliers are equally critical. Some high-risk suppliers need backup plans, while others can be replaced easily. The Kraljic Matrix provides a structured way to classify suppliers based on their impact on the business and risk level.
Kraljic Matrix
The Kraljic Matrix segments suppliers into four categories: Strategic, Bottleneck, Leverage, and Non-Critical. Understanding where each supplier fits helps determine the right risk mitigation strategies.
Action Plan:
- Classify all suppliers using the Kraljic Matrix to identify the most critical risks.
- Secure alternative suppliers and emergency inventory for high-risk categories.
Step 3: Build Redundancy & Flexibility (Sheffi’s Resilience Model)
Resilience is built on three fundamental pillars: Redundancy, Flexibility, and a Resilience Culture. The Sheffi Resilience Framework provides a structured way to balance these components.
Sheffi’s Resilience Framework
Sheffi’s model suggests that true resilience comes from a balanced approach. Too much redundancy increases costs, while too little flexibility makes companies vulnerable. A strong resilience culture ensures rapid adaptation.
Action Plan:
- Identify key single points of failure and increase redundancy where necessary.
- Train teams to handle supply chain disruptions in real-time.
Step 4: Use Network Science to Prevent Domino Effects
Supply chains aren’t linear—they are networks. Some nodes are more connected than others, making failures ripple through the system. Network Science helps map out dependencies and optimize supply chain design.
Network Science & Supply Chain Resilience
A centralized supply chain is vulnerable—if one hub fails, the entire network collapses. In contrast, a decentralized supply chain is more robust, as risks are spread across multiple nodes.
Action Plan:
- Map out critical dependencies (Who depends on whom?)
- Reduce over-reliance on single hubs and spread risk across locations.
Step 5: Accelerate Response with the OODA Loop
When disruption happens, speed matters. The OODA Loop (Observe, Orient, Decide, Act), originally developed for military strategy, is crucial for rapid decision-making in supply chains.
OODA Loop & Supply Chain Decision-Making
Companies that observe disruptions early, orient their response effectively, decide quickly, and act decisively gain a competitive advantage.
Action Plan:
- Implement real-time monitoring for supplier risks.
- Set up an automated early warning system to trigger fast decision-making.
Conclusion: From Fragility to Antifragility – A Call to Action
Supply chains can’t eliminate risk, but they can absorb shocks – if they are designed correctly.
By following these five steps, you can turn resilience from a buzzword into a competitive advantage.