The story behind clay modelling - and why it's still used today
Clay models shaped how cars looked – and are still used by manufacturers today In an age when nearly everything we do relies on digital technology, clay models are still crucial for car designers. The reason is simply that while computer-aided design now leads to amazingly realistic 3D imagery, a physical manifestation of designers’ drawings is easier for them to visualise and evaluate. Clay modelling was introduced to the car industry way back in the 1930s by influential General Motors styling chief Harley Earl. Until then, car design had been a much more difficult and time-consuming affair of wood and metal. Clay modelling took on an even more important role as cars moved from body-on-frame to monocoque construction, as Autocar’s then technical editor Montague Tombs and technical artist Max Millar discovered on a 1945 visit to Longbridge, where the ‘back-room boys’ were hard at work on Austin’s first post-war models. “It is so easy for anyone to sit down and sketch out a ravishing two-seater sports car with an indefinite wheelbase and guesswork accommodation for human beings. But it requires real genius to lay out a practical four-seater saloon on a 7ft wheelbase and still contrive to make the result look universally attractive to the human eye,” wrote Tombs. He described the creative portion of the circa-four-year process, from the board asking for a new design to the first car leaving the factory. “The body designer (BD) starts by preparing a number of bold rough sketches, illustrating various styles and modes, from the orthodox with improvements to the futuristic. These sketches are considered by the management, and one or two will be selected for further development. Then the BD makes a first set of scale drawings, showing side, plan and end views. From this he develops his first scale drawings. “Actual modelling is the next step. Models to the same scale as the drawings are worked out in Plasticine and the curves denoted by the flat views are translated into surfaces which can be viewed from all angles. Enjoy full access to the complete Autocar archive at the magazineshop.com It is only in this way that the main proportions can be seen and balanced, and that the high lights can be seen and, if scattered, brought into continuity by a deft touch here and there. “Probably the BD will make half a dozen models for one design, with slight differences between them, in search for the happiest combinations. And he must not for one instant relax his attention to the irreducible dimensions of seating capacity, and of mechanism also, that lie beneath the surfaces. “And all the time the BD is working he has to bear in mind the possibilities of producing in sheet steel the curves he is outlining. “For a good many reasons connected with visibility and accessibility, the narrowing down of the heavy mass of a saloon body to a fine front, whilst not forgetting that the motoring world is still a trifle ‘radiator-conscious’, causes the treatment of the front end to become one of the most difficult parts of the design. For that reason, the front end of the model is often made detachable, and a series of different front ends can be applied. “When at last the BD has satisfied himself, the steel-pressing expert has given his blessing and the body-engineering chiefs have approved the main details, the sample models are submitted to the directors. "Possibly every point they have in mind is not completely met and further modelling is necessary. In the end, a model is selected for development to the next stages. “A preliminary set of full-size scale drawings is prepared, from which a full-size ‘mock-up’ model will be made. It is made of timber, in blocks so put together that parts can be removed or reshaped. “When the mock-up has been gone over with a fine-tooth comb by everyone concerned, the heavy guns come into action. “The pressed-steel engineer takes a survey of all the panels, wings and other oddments, decides which can be made in a single pressing, which can be divided and where joined. “From this point, evolution goes over to the body drawing office, where complete sets of production drawings are made of every detail, large or small, for the whole job.” It’s amazing, really, that while everything in the car industry has changed a lot over the past 80 years, design is, in essence, as it ever was.
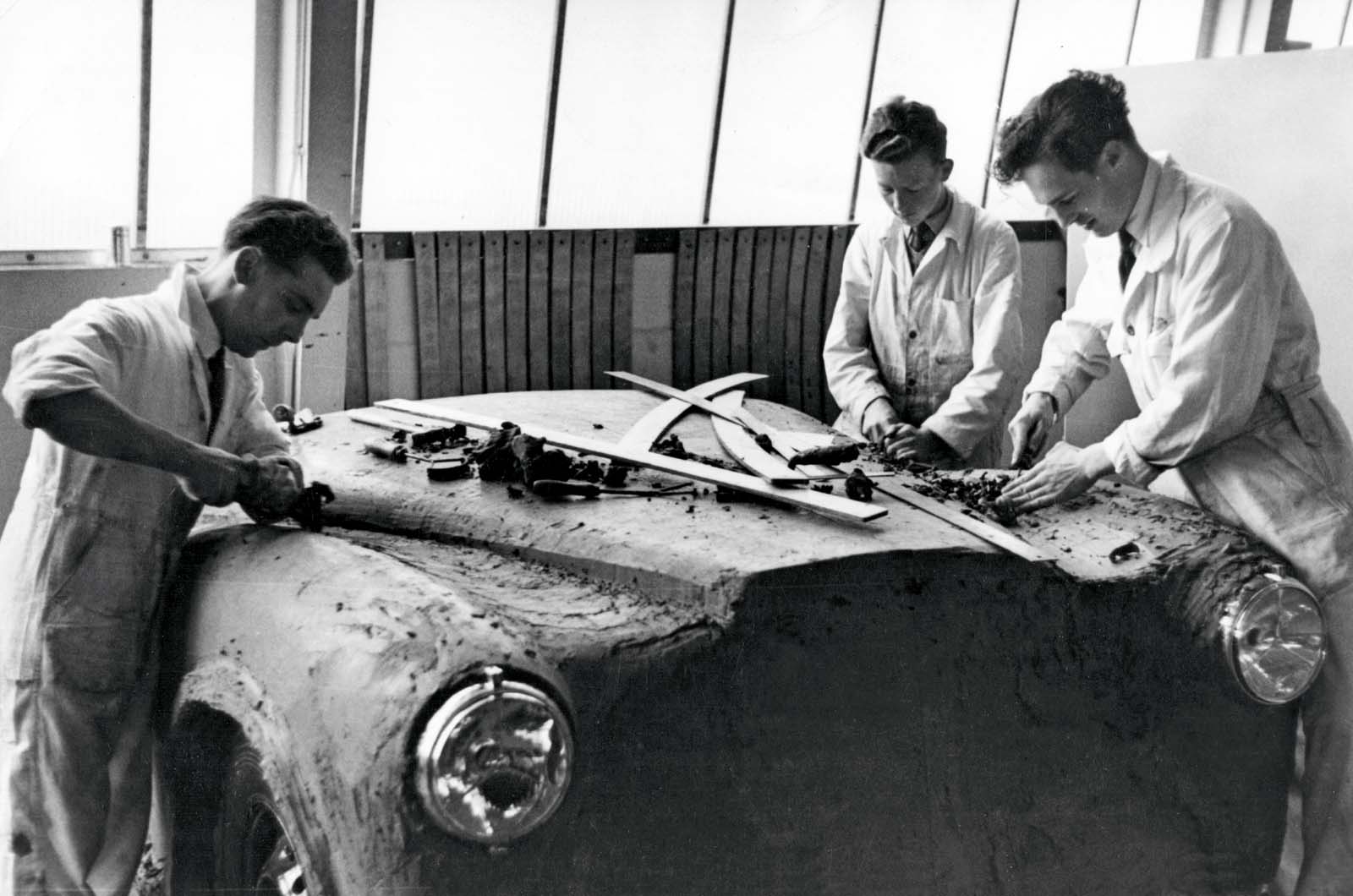
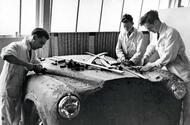
In an age when nearly everything we do relies on digital technology, clay models are still crucial for car designers.
The reason is simply that while computer-aided design now leads to amazingly realistic 3D imagery, a physical manifestation of designers’ drawings is easier for them to visualise and evaluate.
Clay modelling was introduced to the car industry way back in the 1930s by influential General Motors styling chief Harley Earl. Until then, car design had been a much more difficult and time-consuming affair of wood and metal.
Clay modelling took on an even more important role as cars moved from body-on-frame to monocoque construction, as Autocar’s then technical editor Montague Tombs and technical artist Max Millar discovered on a 1945 visit to Longbridge, where the ‘back-room boys’ were hard at work on Austin’s first post-war models.
“It is so easy for anyone to sit down and sketch out a ravishing two-seater sports car with an indefinite wheelbase and guesswork accommodation for human beings.
But it requires real genius to lay out a practical four-seater saloon on a 7ft wheelbase and still contrive to make the result look universally attractive to the human eye,” wrote Tombs.
He described the creative portion of the circa-four-year process, from the board asking for a new design to the first car leaving the factory.
“The body designer (BD) starts by preparing a number of bold rough sketches, illustrating various styles and modes, from the orthodox with improvements to the futuristic.
These sketches are considered by the management, and one or two will be selected for further development. Then the BD makes a first set of scale drawings, showing side, plan and end views. From this he develops his first scale drawings.
“Actual modelling is the next step. Models to the same scale as the drawings are worked out in Plasticine and the curves denoted by the flat views are translated into surfaces which can be viewed from all angles.
Enjoy full access to the complete Autocar archive at the magazineshop.com
It is only in this way that the main proportions can be seen and balanced, and that the high lights can be seen and, if scattered, brought into continuity by a deft touch here and there.
“Probably the BD will make half a dozen models for one design, with slight differences between them, in search for the happiest combinations. And he must not for one instant relax his attention to the irreducible dimensions of seating capacity, and of mechanism also, that lie beneath the surfaces.
“And all the time the BD is working he has to bear in mind the possibilities of producing in sheet steel the curves he is outlining.
“For a good many reasons connected with visibility and accessibility, the narrowing down of the heavy mass of a saloon body to a fine front, whilst not forgetting that the motoring world is still a trifle ‘radiator-conscious’, causes the treatment of the front end to become one of the most difficult parts of the design. For that reason, the front end of the model is often made detachable, and a series of different front ends can be applied.
“When at last the BD has satisfied himself, the steel-pressing expert has given his blessing and the body-engineering chiefs have approved the main details, the sample models are submitted to the directors.
"Possibly every point they have in mind is not completely met and further modelling is necessary. In the end, a model is selected for development to the next stages.
“A preliminary set of full-size scale drawings is prepared, from which a full-size ‘mock-up’ model will be made. It is made of timber, in blocks so put together that parts can be removed or reshaped.
“When the mock-up has been gone over with a fine-tooth comb by everyone concerned, the heavy guns come into action.
“The pressed-steel engineer takes a survey of all the panels, wings and other oddments, decides which can be made in a single pressing, which can be divided and where joined.
“From this point, evolution goes over to the body drawing office, where complete sets of production drawings are made of every detail, large or small, for the whole job.”
It’s amazing, really, that while everything in the car industry has changed a lot over the past 80 years, design is, in essence, as it ever was.