Celanese Leads the Pack When it Comes to Agentic AI
According to a survey by ARC Advisory Group, only 10% of industrial companies are ready to apply artificial intelligence/machine learning. The percentage of industrial companies broadly applying agentic AI and generative AI would be a small fraction of that number. Celanese is an exception. ARC has been actively studying industrial AI for over two years. […] The post Celanese Leads the Pack When it Comes to Agentic AI appeared first on Logistics Viewpoints.
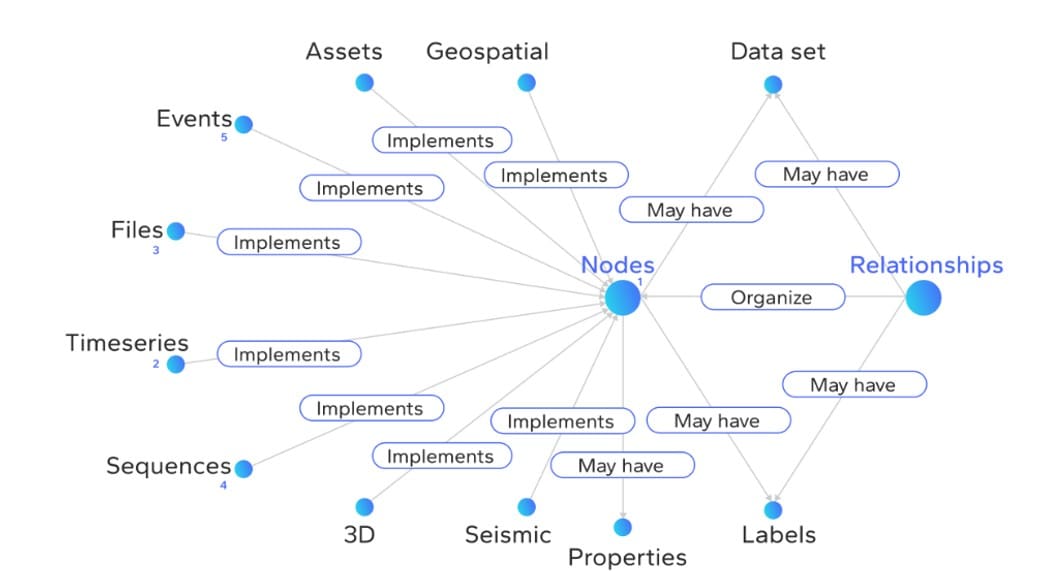
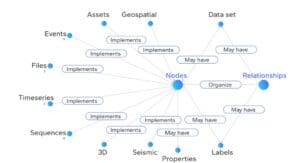
According to a survey by ARC Advisory Group, only 10% of industrial companies are ready to apply artificial intelligence/machine learning. The percentage of industrial companies broadly applying agentic AI and generative AI would be a small fraction of that number.
Celanese is an exception. ARC has been actively studying industrial AI for over two years. What Celanese has accomplished is the single best example ARC is aware of employing agentic AI and copilots at scale. Ibrahim Al Syed, the director of digital manufacturing at Celanese, was surprisingly forthcoming about how Celanese developed these capabilities at ARC Advisory Group’s 29th Annual ARC Industry Leadership Forum. He also spoke at the ARC forum in 2023, and this article is based on that presentation as well.
Agentic AI involves creating a system of interacting agents, each trained on a specific task or dataset. These agents can communicate, negotiate, and collaborate to solve complex problems. Agentic allows for much greater flexibility. Instead of relying solely on a single, monolithic AI model (based on a massive large language model), a company can orchestrate a team of specialized agents, each leveraging the best AI or mathematical technique for its specific task. generative AI is starting to be used as the orchestra director that weaves these agents together in a process flow and provides a uniform “co-pilot” style user interface.
The Celanese Supply Chain
Celanese Corporation (NYSE: CE), headquartered in Dallas, Texas, is a global chemical and specialty materials company with revenues of over $10 billion. The company operates in over 20 countries and has over 12,000 employees. The company has 55 manufacturing sites across the world. The company runs some plants, and some are operated by third parties.
The chemical industry has a complex supply chain. Their plants are very expensive. Maximizing factory throughput is critical. Further, multiple plants may be capable of making the same product, and figuring out which plant should produce the product based on the current supply and demand situation is not straightforward.
Chemical companies are extremely safety conscious. They must be. The risks associated with chemical manufacturing include the storage and transportation of raw materials, finished products, and waste. These hazards include, among other things, pipeline and storage tank leaks and ruptures, explosions and fires, and discharges or releases of toxic or hazardous substances. The occurrence of any of these events disrupts the global supply chain and can deeply impact profitability.
Building the Foundation
During COVID-19, Celanese began to think about the need for a digital transformation. Travel restrictions made it difficult to staff their plants. The ability to have a digital platform that supported workers who could help run their plants from remote locations was seen as highly desirable. Further, when they began thinking about a platform to detect and react to equipment anomalies, they realized those capabilities would support safety, better product quality, and production optimization. They realized the ROI associated with that could be massive.
At this point, they were not thinking about agentic AI, no company was, but the platform they put in place turned out to be perfect for agentic AI, and AI became a big goal in their digital transformation.
Celanese was also not looking to take humans out of the loop. Their guiding principle was human-centric digital design. For example, if an asset issue was detected, solving that issue could involve multiple applications used by multiple people, seeing different information, entering different data, bouncing emails and texts back and forth, and moving information from one place to another. “One event could create so much churn,” Mr. Al Syed explained.
A person at a manufacturing facility is involved in all kinds of processes, Mr. Al Syed elaborated. They prepare equipment for maintenance, do isolation (disconnect a piece of equipment from the flow of chemicals by closing valves), look at quality or reliability metrics, and do rounds. People-centered design focuses on distinct roles so that “every day we allow people to work at their maximum potential.”
“We needed to model the data in a way that we can do simple searching. Can I have an industrial Google at a manufacturing facility? Why is it so hard for our people to find information in the right context? We spent hours and hours looking for data, whether it was for audits, compliance, or just basic troubleshooting. This became an investment priority.”
In the past, if the business had a need, they would buy an application. Then, another application would be purchased, and another, and another. This ends in a spaghetti approach to data integration. Data does not move. Managing those applications becomes more challenging. Celanese recognized a need to decouple their data away from their applications. Data should be created once and move seamlessly, in real-time, to where needed. This architecture was necessary to create a unified experience for users.
Data must be modeled consistently across the organization. How data is created, used, and maintained must be standardized. Data governance is critical. This, Mr. Al Syed said, is key in moving from an incremental application ROI to bigger, more strategic forms of value creation.
Celanese chose the Data Fusion platform from Cognite as their industrial data platform. Increasingly what Cognite is offering is called a data fabric; in their case, it is a data fabric for plant-level data. Industrial data is voluminous. Celanese has 2.5 trillion records from 47 data sources in the Cognite platform. Industrial data is also more complex than enterprise data. Plant-level data includes time series data from sensors and machines, transactional data – like orders, and unstructured data from engineering drawings and pictures.
A data fabric speeds and simplifies access to data assets across the business. It accesses, transforms, and harmonizes data from multiple sources to make it usable and actionable for various business use cases.
Building Context
Celanese’s goal around human-centered design was to surface the correct data, with the proper context, to the right person, at the right time to make better decisions. But then people need to act. The ability to act on the information must be part of the workflow.
But getting the context right is a difficult problem. Contextualization is the process of identifying and representing relationships between data to mirror the relationships that exist between data elements in the physical world.
This is where knowledge graphs are being used. Cognite’s platform includes a knowledge graph. A knowledge graph creates relationships across previously siloed data sources. Knowledge graphs “weave” together a unified, seamless layer for data management and, by doing this, often uncover hidden patterns and relationships, patterns no human could detect. Answering a question like “Why has this piece of equipment gone down?” can require accessing many pieces of siloed data and then looking for relationships between the data sets and an event that has occurred. Knowledge graphs can find relationships that no human could uncover.
JO.AI, a Co-pilot for the Plant
JO.AI is the user interface. It is built on Generative AI. Generative AI is an artificial intelligence technology that can produce various types of content, including text, imagery, and audio. It turns out that the way to use GenAI is as an advanced user interface. At Celanese, JO.AI is the single point of interaction that facilitates workers in getting their work done.
JO.AI was built quickly. That was only possible because Celanese had the right foundation in place – they had cleaned their data, improved data governance, put in an industrial data fabric, and then used a knowledge graph to contextualize the data.
Mr. Al Syed demoed several use cases. They were beautiful demos. In one demo, a system detected an asset that was not performing right. A user is assigned to examine this. The user asked to see a piping and instrumentation diagram and then wanted to see the work orders for the vessel in question and the tag for that vessel. JO.AI provided these. The manager then assigned Fred the job of diagnosing the problem. The manager used JO.AI to create a work order for Fred. Fred then uses the interface to diagnose the issue. JO.AI asks, “Do you see this? Is this happening?” JO.AI even looked at a picture of the asset taken on Fred’s phone. Then based on the picture and the answers, JO.AI suggested that corrosion might be the problem. Fred agrees. Then a new updated work order was created to swap out the asset.
Radix, a consultant and system integration firm, helped to develop JO.AI. Pre-trained AI agents focused on specific use cases for specific user personas were created. Use cases focused on four key areas:
Optimized Operator Rounds: JO.AI provides insights that ensure operations teams are focusing their rounds on the proper checklists.
Data-Driven Checklist Management: The interface recommends the optimal frequency of checklist items, identifies areas with high-volume issues, and highlights deviations.
Balanced Workloads: JO.AI helps ensure the checklist workload is appropriate for each shift.
Streamlined Maintenance: The solution facilitates maintenance and work notification opportunities, recommends resource plans, and assists operators in writing work orders.
JO.AI was built in phases. First, it was piloted at one process unit at one plant. Then, gradually, the use cases expanded to over 40, and the number of plants using JO.AI increased to 50.
Mr. Al Syed did not talk in detail about the ROI, except to say it was significant and would continue to grow. He did give one example, their ability to do effective preventative maintenance did increase by 15%.
He also said JO.AI was not perfect. One key area of focus this year is to eliminate hallucinations. “It is better to have no answer than the wrong answer.”
Amazingly, this journey was accomplished in just three and a half years. In part, this was skill. Celanese focused first on building the right foundation. But there was also an element of luck. Cognite evolved from a robust industrial data platform to also being an AI platform just in time for Celanese to take advantage of it.
The post Celanese Leads the Pack When it Comes to Agentic AI appeared first on Logistics Viewpoints.