No Balloons Needed: Practical Moves to Navigate Tariff Volatility
The manufacturing sector is facing unprecedented volatility in global trade, with tariffs becoming the latest in a series of uncertainty drivers that are impacting virtually all industries. Trade policies are constantly evolving, forcing companies to assess how these changes impact customer demand, supply networks, fulfillment strategies, and cost to serve. Supply chains need to be […] The post No Balloons Needed: Practical Moves to Navigate Tariff Volatility appeared first on Logistics Viewpoints.
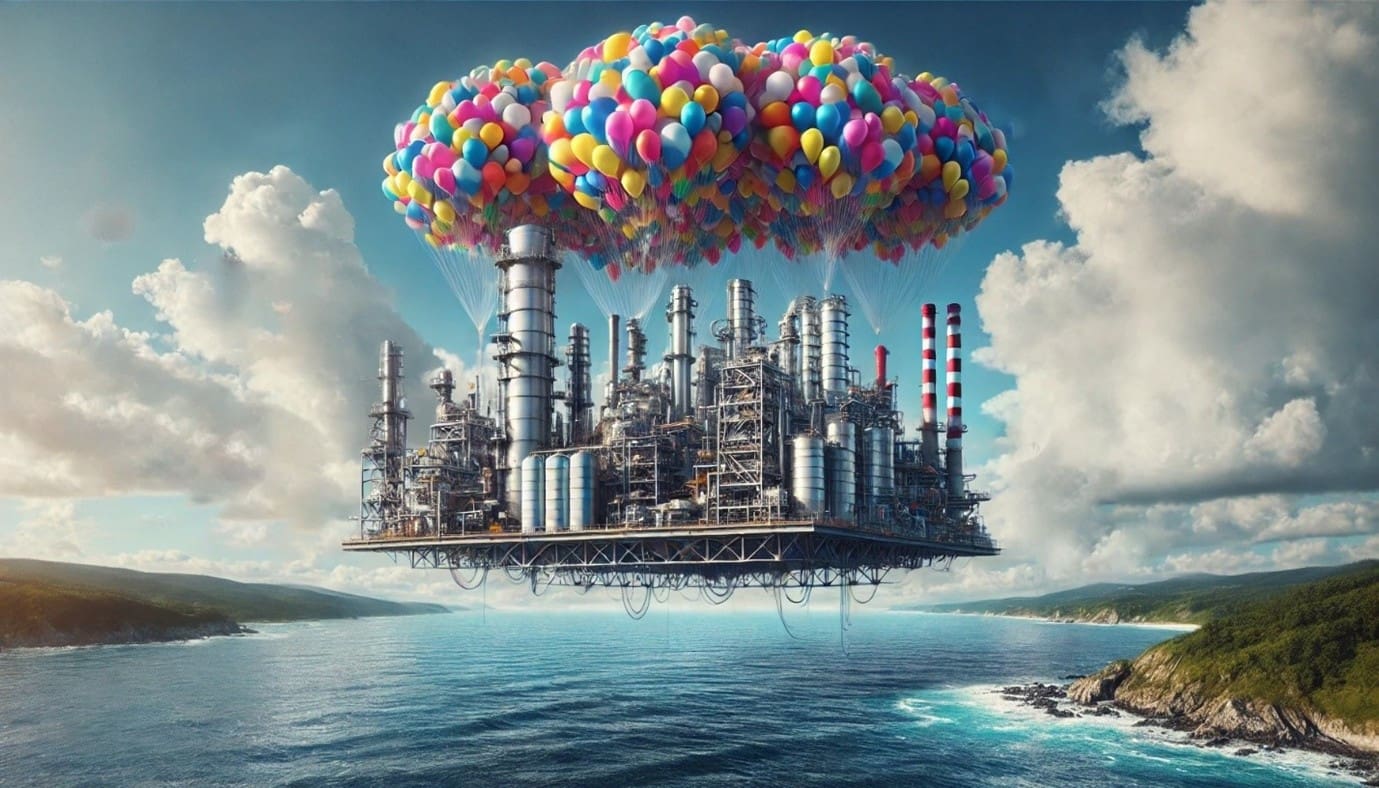
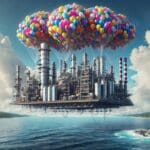
The manufacturing sector is facing unprecedented volatility in global trade, with tariffs becoming the latest in a series of uncertainty drivers that are impacting virtually all industries. Trade policies are constantly evolving, forcing companies to assess how these changes impact customer demand, supply networks, fulfillment strategies, and cost to serve. Supply chains need to be more agile than ever, yet much of the advice circulating in the industry remains high-level or less than ideal.
There’s no shortage of commentary on how companies should respond — move production, shift suppliers, and reconfigure operations are just a few common recommendations. But are these truly actionable in the short term?
The reality is, you can’t just uproot a manufacturing facility and move it overnight, as if it were the floating house in the movie Up, carried away by a bunch of balloons. Manufacturing plants are deeply entrenched; tied to infrastructure, suppliers, skilled labor, and regulatory requirements. Moving them may be an option, but it’s neither a quick fix nor the most practical first step in responding to tariff volatility.
So, what can supply chain leaders do right now? Instead of broad, theoretical solutions, we need to go deeper and identify the tangible levers companies can pull to adapt. There are actions within a supply chain’s control that can make a real impact without requiring an overnight transformation, and that provide agility, flexibility, and resilience in the face of uncertainty.
Companies must take a pragmatic approach — leveraging supply chain planning technology and strategic decision-making to effectively navigate tariff volatility and uncertainty.
A Lesson in Tariff-Induced Disruption
Consider a North American textile manufacturer that was caught off guard by a 25% tariff on Canadian goods imported into the U.S. This increase, combined with existing duties, made it unviable financially to serve American customers which made up 80% of revenue. The company, heavily invested in Canadian manufacturing, faced a crisis because its raw materials were sourced from outside North America, disqualifying it from USMCA tariff exemptions.
As a result, the company had to lay off workers and reevaluate its entire strategy – even as tariffs are paused – due to a lack of supply chain flexibility. To mitigate such risks, manufacturers need to learn from others and look at how they can:
- Diversify sourcing strategies to include (in this case) North American suppliers.
- Diversify customer base outside of United States to avoid tariffs on broader sales base.
- Establish inventory reserves in key markets to avoid supply chain disruptions.
- Develop financial flexibility by securing capital and implementing cost-cutting measures.
- Design product flexibility to include materials sourced for US and non-US markets or quickly adapt to different sources of materials.
Strengthening the Supply Chain
Supply chains must embrace agility, where companies proactively adjust and optimize their customer, product and network strategies to maximize opportunity – as opposed to fragility – where uncertainty leads to disruptions and chaos. This shift goes hand-in-hand with the need to build tighter orchestration, collaboration & automation to enhance decision-making to quickly respond to changes.
A key approach is to deploy options-based plans as certainty or conditions fluctuate. These plans are created by:
- Predicting a range of uncertainty across demand, supply and disruptions, and then create range-based policies to quickly respond to these changes.
- Stress-testing, evaluating scenario outcomes to identify and assess options to address different ranges of conditions.
- Leveraging probabilistic plans to identify and assess options, and generate range-based policies, rules & thresholds.
Practical Strategies for Managing Tariff Volatility
1. Evaluate Nearshoring / Onshoring and Multisourcing
Relying on a single country or supplier exposes manufacturers to tariff risks. Companies should explore nearshoring strategies to relocate production, or dual/multisourcing initiatives, working with multiple suppliers across different regions.
However, shifting suppliers requires careful ROI evaluation of cost, quality, and lead time considerations to avoid redundancy, especially where it does not add adaptability.
2. Leverage Foreign Trade Zones (FTZs) and Pre-Buying Strategies
Manufacturers can mitigate tariff impacts by strategically managing inventory.
Foreign Trade Zones (FTZs) represent a viable option for companies to store goods without incurring tariffs until they are moved into domestic markets. This allows for more strategic duty payments and improved cash flow opportunities.
Pre-Buying Inventory is another option, allowing companies to purchase additional stock before tariff hikes take effect to minimize short-term cost increases.
Advanced supply chain planning software enables organizations to optimize the entire network holistically (MEIO) as well as model FTZ (within an existing facility or separate location), balancing stock levels and moving inventory based on demand fluctuations and tariff schedules.
3. Take Control of Purchase Prices
Hedging strategies which may include mid to long-term price arrangements help provide financial stability amid tariff fluctuations. These may include:
- Long-term supplier agreements to lock in favorable pricing.
- Spot-buying strategies to capitalize on market softening.
Many companies take advantage of vertical integration of the value chain, to have more direct control of their supply chain and reduce dependency on external suppliers.
These strategies include taking advantage of scenario planning, allowing teams to select certain suppliers or quantities based on current market conditions.
4. Flexible Production and Product Redesign
Tariff-driven cost increases may force companies to reevaluate production strategies:
- Redesign products using alternative materials sourced from lower-tariff regions.
- Add product flexibility to sell with differently sourced material based on sales region.
- Retire non-competitive products that are no longer viable under new trade conditions.
Additionally, leading companies orchestrate and collaborate on production needs with suppliers to reduce lead-times and minimize inventory levels to mitigate impact of higher costs across partners.
5. Platform Revisions to Material Sourcing
Re-evaluating Bills of Materials (BOMs) and redesigning sourcing strategies can help reduce reliance on high-tariff regions. Instead of simply stockpiling materials or accepting increased costs, manufacturers should explore ways to substitute materials, adjust sourcing locations, and optimize product designs to create more tariff-resilient supply chains.
Standardizing materials across multiple products can enable greater flexibility in supplier selection and procurement.
Companies should aim to build flexibility into their recipes and product designs, allowing them to adapt sourcing based on shifting trade policies without compromising quality or compliance.
Key Takeaways
The uncertainty surrounding tariffs is a microcosm of the broader unpredictability in global supply chains. But the increasing complexity presents opportunities for companies to drive innovation and resilience. It’s paramount to take proactive measures to shape your supply chain using strategic foresight and advanced planning technology.
To navigate tariff uncertainty, companies must embrace agility by leveraging scenario planning, to drive decision-making and gain a competitive edge.
About the author
Matt Hoffman is the Vice President of Product and Industry Solutions at John Galt Solutions. Matt specializes in delivering transformational from analysis through execution across a diverse range of clients in manufacturing, distribution, and retail. Matt is committed to ensuring that processes drive solution adoption, resulting in measurable outcomes. Throughout his career, Matt has successfully led software implementations utilizing best-in-class supply chain planning systems, execution systems, and merchandising planning systems.
The post No Balloons Needed: Practical Moves to Navigate Tariff Volatility appeared first on Logistics Viewpoints.