Inside Cosworth: how Brit firm is keeping the screaming V12 alive
Commerical director Chris Willoughby shows us around the Cosworth factory... The company faded from popular view for a while but is now back at the forefront, designing soul-stirring engines Features such as this so often open with a somewhat clichéd remark about the incongruousness of the drab surroundings from which the renowned company under the spotlight operates. True to form, we find the headquarters of one of Britain’s best-known and most influential automotive engineering outfits nestled between the garages and warehouses of Northampton’s sprawling St James Industrial Estate. Head to the right of Jewsons and around the Royal Mail sorting office to find the main office entrance, and then up and under the West Coast mainline and past the MOT centre for the factory itself. This small and unassuming complex of buildings forms what could undramatically be described as the epicentre of Britain’s motorsport and performance car engineering heritage. The history of Cosworth Engineering is so intrinsically connected with that of British sports cars that you have to wonder what today’s car world would look like had founders Mike Costin and Keith Duckworth never formed a relationship while working at Colin Chapman’s fledgling Lotus Engineering outfit in the late 1950s. From humble beginnings in grassroots motorsport, the pair evolved their business into a leading engine supplier for top-flight motorsport series, famously creating the most successful engine in the history of Formula 1, the DFV V8. The business would go on to put its name to some of the most revered and influential performance cars of the late 20th century: Ford's Escort and Sierra, Mercedes-Benz 190E, Audi RS4, Subaru Impreza… The list goes on, and today the company counts in its portfolio some of the most powerful and expensive road cars currently in production: the likes of Bugatti, Aston Martin and Gordon Murray have all turned to the storied outfit for a new generation of mammoth-capacity motors. Commercial director Chris Willoughby has been at Cosworth for 34 years, first as an engineer in the F1 powertrain division – what he calls a “golden era”, during which he worked with legends including Senna and Schumacher. Now he oversees a team that builds some of today’s biggest and most beautiful road car engines. While the remit has changed dramatically, the ethos has not, and Willoughby says the pit lane mentality remains absolutely central to Cosworth’s success. “I can see parallels between that really successful racing era and where we are now with the hypercars,” he says. Primarily this is reflected in how self-contained and agile the business still is – a characteristic fostered by its involvement in those halcyon days of F1, when engineering innovation and rapid reaction times were utterly crucial to supremacy. “All of our customers today want shorter and shorter programmes, so we’re very focused on that,” continues Willoughby. “But being vertically integrated is very much who we still are. "An interesting parallel with the DFV is that we made getting on for 1000 of them, and if you look at some of the car programmes we’re working on now, we’re certainly going to be into the many hundreds of engines. Creating a clean-sheet design, developing and then manufacturing it in quantity – that was our business model back then, and that’s our business model now.” What’s different about Cosworth’s output now, though, is that the engines are so much more than mere tools used in the pursuit of racing success. Rather, they are upheld as mechanical marvels in themselves, ones that are central to the appeal – and ultra-exclusive billing – of the cars in which they are mounted. “There’s an appreciation of the engines and vehicles almost like they are pieces of art,” says Willoughby. “They’re appreciated in the same way – even the aesthetic of the engines and what they look like is very important. And I think there’s a growing interest in what the engines are technically beneath the skin. “People are blown away when they see a piston or a crankshaft, or the oil cooling squirt jets… All those things – there seems to be a real appetite for that now.” Willoughby echoes the sentiments of Bugatti-Rimac CEO Mate Rimac, who said recently that demand for the ludicrously quick Nevera hypercar was flagging as the world’s highest-net-worth individuals were being drawn by the heightened analogue appeal of its combustion-engined contemporaries. That his new Cosworth V16-powered Bugatti hypercar is named Tourbillon – after a tiny and highly intricate mechanism that’s usually on display in expensive watches – is no coincidence. It is largely because of the enduring allure of a mechanical combustion engine – with all of its pulleys, belts, plugs and bangs – that Cosworth is still designing and producing enormous 12- and 16-cylinder engines, and all of this while the more mainstream sectors of the automotive industry scrabble to downsize and decarbonise. But there
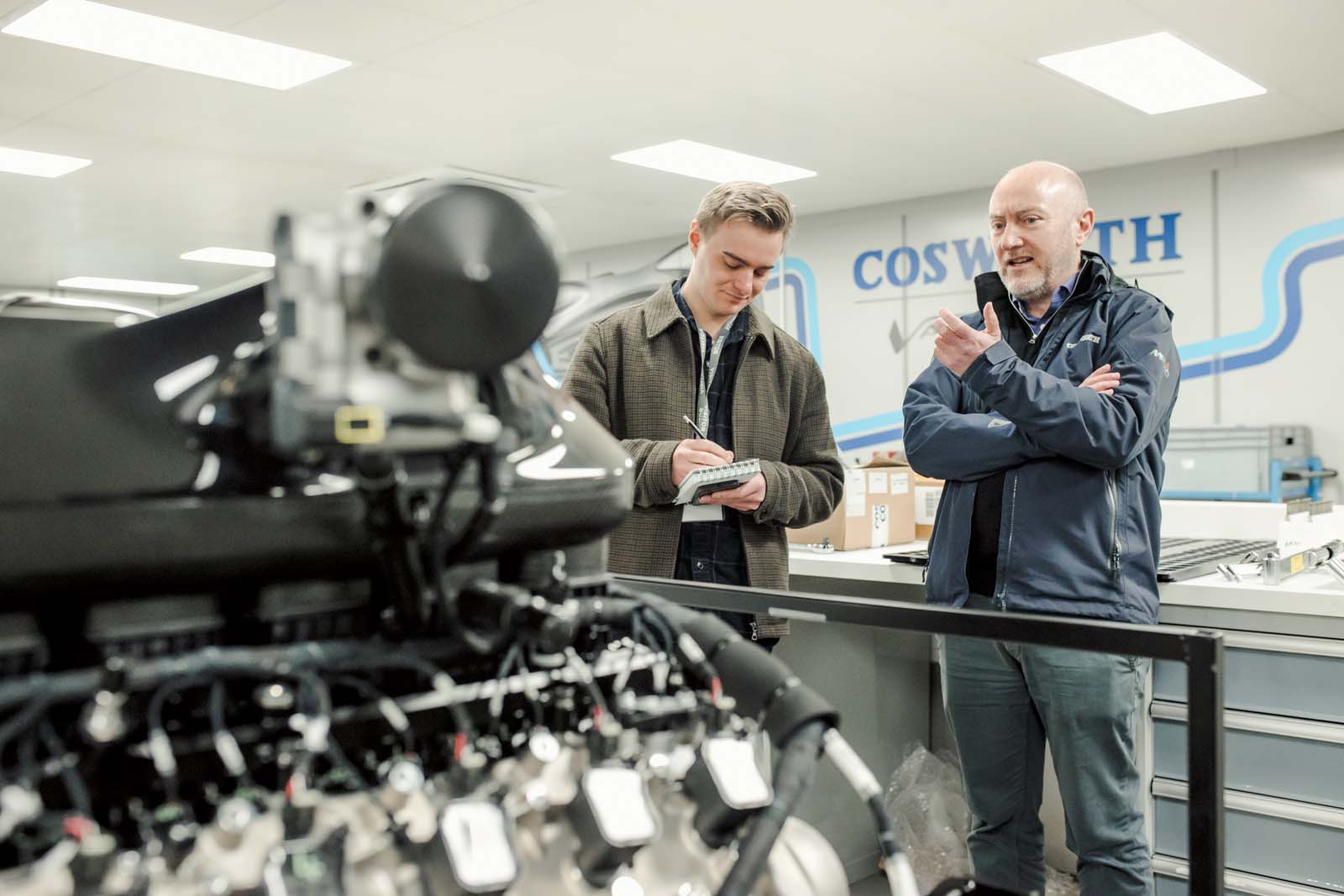
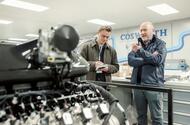
Commerical director Chris Willoughby shows us around the Cosworth factory...The company faded from popular view for a while but is now back at the forefront, designing soul-stirring engines
Features such as this so often open with a somewhat clichéd remark about the incongruousness of the drab surroundings from which the renowned company under the spotlight operates.
True to form, we find the headquarters of one of Britain’s best-known and most influential automotive engineering outfits nestled between the garages and warehouses of Northampton’s sprawling St James Industrial Estate.
Head to the right of Jewsons and around the Royal Mail sorting office to find the main office entrance, and then up and under the West Coast mainline and past the MOT centre for the factory itself.
This small and unassuming complex of buildings forms what could undramatically be described as the epicentre of Britain’s motorsport and performance car engineering heritage.
The history of Cosworth Engineering is so intrinsically connected with that of British sports cars that you have to wonder what today’s car world would look like had founders Mike Costin and Keith Duckworth never formed a relationship while working at Colin Chapman’s fledgling Lotus Engineering outfit in the late 1950s.
From humble beginnings in grassroots motorsport, the pair evolved their business into a leading engine supplier for top-flight motorsport series, famously creating the most successful engine in the history of Formula 1, the DFV V8.
The business would go on to put its name to some of the most revered and influential performance cars of the late 20th century: Ford's Escort and Sierra, Mercedes-Benz 190E, Audi RS4, Subaru Impreza…
The list goes on, and today the company counts in its portfolio some of the most powerful and expensive road cars currently in production: the likes of Bugatti, Aston Martin and Gordon Murray have all turned to the storied outfit for a new generation of mammoth-capacity motors.
Commercial director Chris Willoughby has been at Cosworth for 34 years, first as an engineer in the F1 powertrain division – what he calls a “golden era”, during which he worked with legends including Senna and Schumacher. Now he oversees a team that builds some of today’s biggest and most beautiful road car engines.
While the remit has changed dramatically, the ethos has not, and Willoughby says the pit lane mentality remains absolutely central to Cosworth’s success. “I can see parallels between that really successful racing era and where we are now with the hypercars,” he says.
Primarily this is reflected in how self-contained and agile the business still is – a characteristic fostered by its involvement in those halcyon days of F1, when engineering innovation and rapid reaction times were utterly crucial to supremacy.
“All of our customers today want shorter and shorter programmes, so we’re very focused on that,” continues Willoughby. “But being vertically integrated is very much who we still are.
"An interesting parallel with the DFV is that we made getting on for 1000 of them, and if you look at some of the car programmes we’re working on now, we’re certainly going to be into the many hundreds of engines. Creating a clean-sheet design, developing and then manufacturing it in quantity – that was our business model back then, and that’s our business model now.”
What’s different about Cosworth’s output now, though, is that the engines are so much more than mere tools used in the pursuit of racing success.
Rather, they are upheld as mechanical marvels in themselves, ones that are central to the appeal – and ultra-exclusive billing – of the cars in which they are mounted.
“There’s an appreciation of the engines and vehicles almost like they are pieces of art,” says Willoughby. “They’re appreciated in the same way – even the aesthetic of the engines and what they look like is very important. And I think there’s a growing interest in what the engines are technically beneath the skin.
“People are blown away when they see a piston or a crankshaft, or the oil cooling squirt jets… All those things – there seems to be a real appetite for that now.”
Willoughby echoes the sentiments of Bugatti-Rimac CEO Mate Rimac, who said recently that demand for the ludicrously quick Nevera hypercar was flagging as the world’s highest-net-worth individuals were being drawn by the heightened analogue appeal of its combustion-engined contemporaries.
That his new Cosworth V16-powered Bugatti hypercar is named Tourbillon – after a tiny and highly intricate mechanism that’s usually on display in expensive watches – is no coincidence.
It is largely because of the enduring allure of a mechanical combustion engine – with all of its pulleys, belts, plugs and bangs – that Cosworth is still designing and producing enormous 12- and 16-cylinder engines, and all of this while the more mainstream sectors of the automotive industry scrabble to downsize and decarbonise.
But there are also more rational technical considerations to bear in mind. Today, the viability of using batteries in such high-performance cars as the Valkyrie and T50 is limited, because the energy density “is not there”, says Willoughby. “They will progress and get better, but doing 10 laps of the Nürburgring seems like a long way off.
“If you want to do 10 laps in a car that weighs 1000kg and has desirable dynamic qualities to it, then an engine is still very much the tool to use.”
Hence Cosworth’s exploration of alternative means of fuelling the internal combustion process. The study has yielded promising results, lending further weight to the growing argument that banning engines themselves – rather than the highly polluting substances that currently make them spin – is a misguided enterprise.
Willoughby adds: “We’ve been running synthetic fuels for four or five years, and the chemists say it’s exactly the same as gasoline. Sure enough, when we put it in an engine, we can’t tell the difference.”
He acknowledges that production of synthetic fuels is currently highly limited, and thus it is prohibitively expensive for use in a mainstream context. “But for our type of applications,” he says – referring to the £3.2 million Tourbillon and £2.8 million T50, for example – “the price is less likely to be a limiting factor.”
The fact that racing at the Goodwood Revival is now powered by e-fuels, and that F1 is on track to follow suit in 2026, is representative of the opportunity at hand to decarbonise those enthusiast-facing sectors of the automotive world that simply can’t – at least yet – feasibly switch to battery power.
In one of Cosworth’s 10 top-secret dyno suites, one engine has been rigged up to burn hydrogen. Willoughby says it has also shown promise as an alternative fuel because of its propensity to burn over a wide air-fuel ratio range and produce comparable power outputs to petrol.
Dampening its appeal over purpose-designed synthetic fuels, though, is that it requires around 10 times more storage space in the car and produces water, which “all ends up somewhere”, necessitating extensive moisture-capture modifications – as demonstrated by the labyrinthine pipework twisting its way up from the manifold of this block into the vents on the ceiling.
The primary inhibitors to adopting hydrogen for use in combustion engines are not so much the technical limitations but rather the crucial developments that can’t be achieved within the confines of a Northampton workshop. “The adoption of hydrogen depends on lots of things outside of our control,” says Willoughby, “like the development of infrastructure and supply.”
Even if this is not a technology that has a place in today’s world, it may well be needed in the future – and Cosworth will be ready to take to the front of the grid, in figurative terms, when it is.
Cosworth’s efforts at combustion-engine preservation are far from a wilful nosethumbing of the rules and regulations that will bring about the eventual demise of fossil-fuelled powerplants; instead, they come in recognition of the fact that even the very highest echelons of the automotive market will be forced to adapt to new technologies as part of a clean-up act that will safeguard their future. It’s just not entirely clear when that will be, at least for now.
The fact that we’re looking at an engine that burns hydrogen does not mean Cosworth has any immediate plans to commercialise this technology, but rather it serves as testament to the company’s ruthless commitment to being prepared for any eventuality.
“We need to know how to react to changes in the market,” explains Willoughby. “We have to be a bit diversified and understand how our skillset maps into the market, and where it has value.”
As he speaks, Willoughby is forced to raise his voice over the deafening growl of a Gordon Murray V12 that’s running in the adjacent test bay – a neat metaphor for Cosworth’s eggs-in-many-baskets approach.
Small wonder that the people responsible for these screaming mechanical marvels should be exploring ways of keeping their crankshafts spinning into the future.
From the dark and deafening confines of the test benches that are little changed since the company’s early days, we are ushered down a hallway to the final assembly suite, which is comparatively blinding in its surgical spotlessness and lays bare the scale, significance and splendour of Cosworth’s latest generation of combustion engines.
Perhaps it’s the relative mundanity of its surroundings that so emphasises the ludicrous proportions of Bugatti’s new V16, but you get the sense that this is a powerplant conceived to draw the eye organically even when removed from the multimillion-pound missile in which it will be mounted.
Even if you have only the vaguest inkling of which bit does what in an engine, there is pleasure to be drawn from the granite-hewn quality of the components used here, the attention to detail in linking them all together and the sheer size of what they constitute when they are united.
This 8.3-litre lump is so colossal that you don’t so much casually glance around it as embark upon a lap of it: comparisons with the likes of the Rolls-Royce Merlin and the Beast of Turin’s flame-spitting 28-litre motor feel more than appropriate.
Our request to fire the engine up in situ is wrongly assumed to be a joke and laughed off, but videos from testing confirm that it sounds about as biblically cataclysmic as you would expect: guttural and booming, with a baritone bark that spirals upwards in pitch as it approaches its 9000rpm redline.
As it accelerates away from the camera, it sounds almost like two Mercedes-Benz SLR McLarens having a drag race. “Hopefully we can keep it so limiter-free,” said Mate Rimac recently. Quite.
Willoughby says this aural drama was a prerequisite of Bugatti’s V16 programme, which was good news for a company whose co-founder Duckworth is quoted as saying: “Turbos are for people who can’t build engines.”
Here at Cosworth, they like their engine aspiration natural, their revs high and their exhaust notes shrieking. Willoughby, surprisingly perhaps, drives an electric car himself, and says they are “absolutely the right answer” in mainstream applications.
But in the sort of rarified air that Tourbillon, Valkyrie and T50 owners breathe, there is still a huge demand for analogue viscerality and evocative authenticity that can only be provided by a free-breathing, huge-capacity petrol engine.
And while very, very few of us will ever have the opportunity to take one of these automotive artworks up through the rev range ourselves, the resulting soundtracks can at least be enjoyed by anyone within earshot.
“The thing that’s surprised me is how well received the sound of a naturally aspirated engine is,” admits Willoughby. “I think that’s deep-rooted in the human psyche in some way. I’m not a psychologist, but I think it’s hard-coded from when tigers used to jump out on us from behind bushes – we’re coded to have a response to noise.”
There’s rather less poetic licence in that analogy than you might think. When the probing jaw of the Aston Martin Valkyrie emerged from behind the hay bales at the Goodwood hillclimb’s first corner last year and its deafening exhaust note – more than reminiscent of a 1990s F1 car – began to reverberate ominously around West Sussex, the stunned, respectful silence that fell on the Festival of Speed grandstands was testament to the emotional power still wielded by a properly fettled combustion engine.
This roar, though, unlike a tiger’s, attracts a crowd rather than dispels it – but it is also similarly endangered and risks being silenced without the efforts of dedicated preservationists.
Happily, there’s a group of highly skilled and ruthlessly committed engineers in the East Midlands, working hard to ensure it remains unstifled for many years to come.