A ‘Pathfinder’ for the Army: FLRAA will be a first for MOSA in helicopter design
[Sponsored] MOSA and the digital backbone give the Army a vendor-agnostic path to make aircraft system modifications from the outset of Future Vertical Lift.
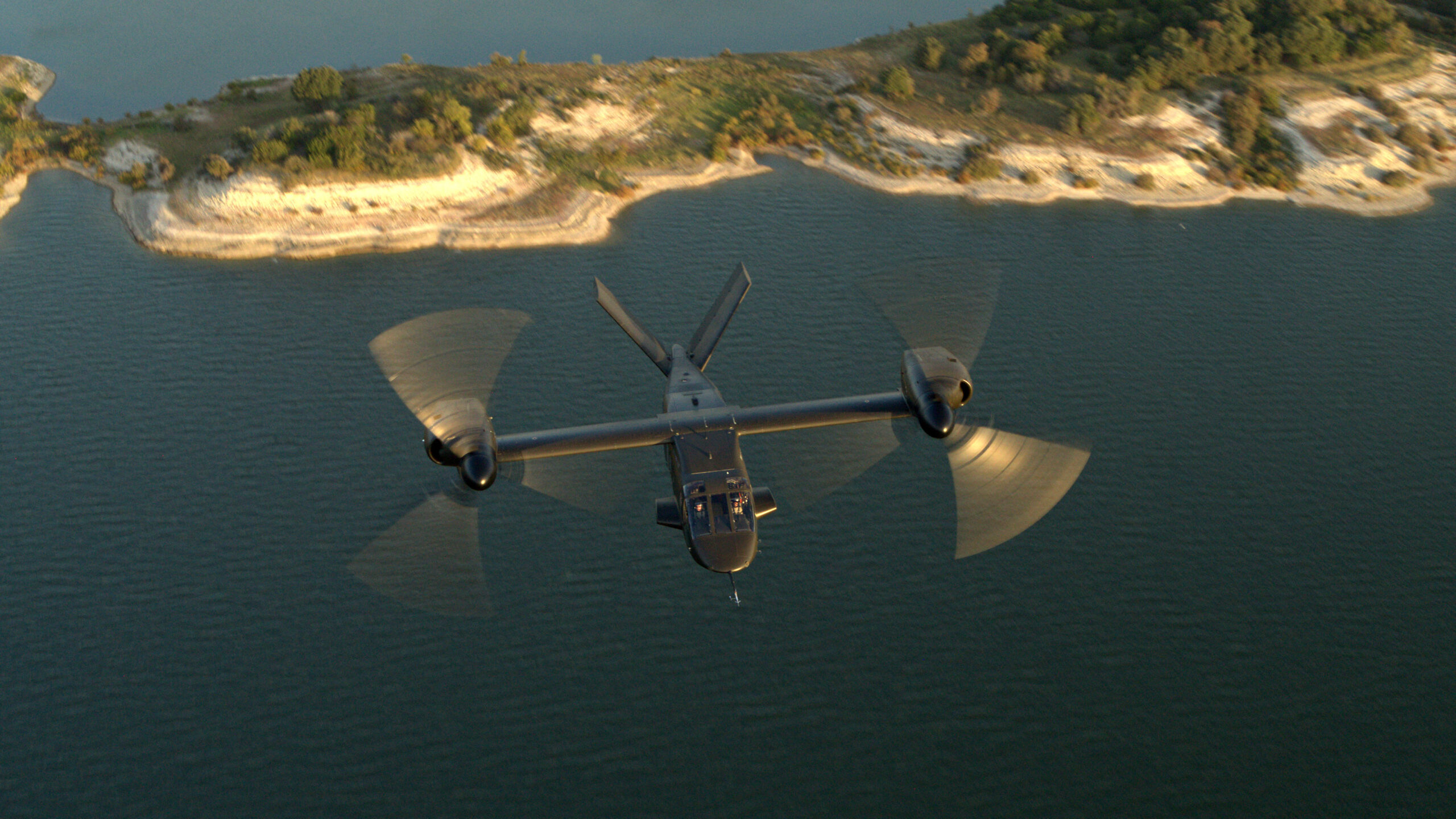
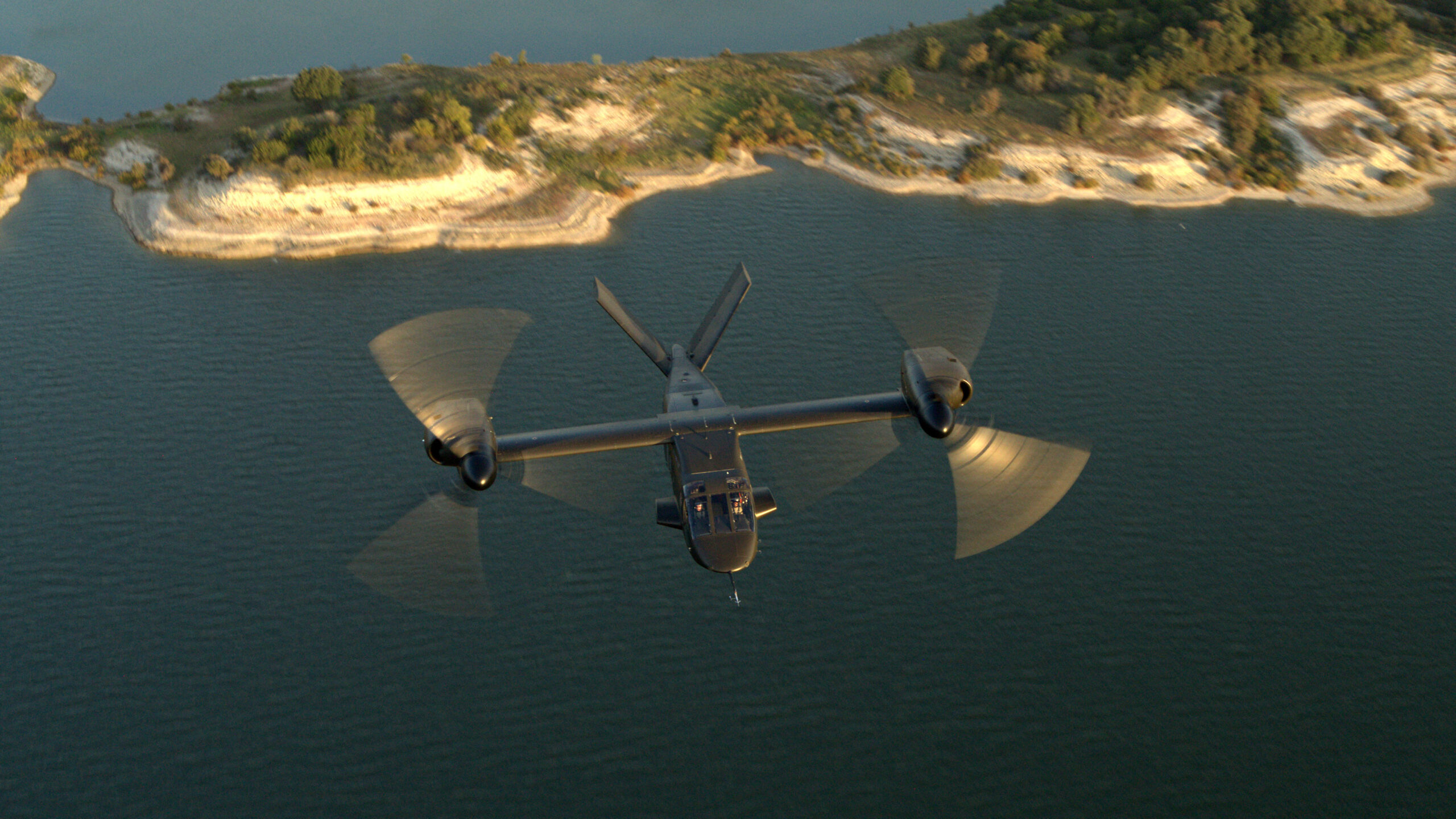
Bell’s FLRAA program showcases how MOSA and the digital backbone can enable rapid upgrades and integration of new technologies. (Bell photo)
The Army’s Future Long Range Assault Aircraft (FLRAA) will not only fly fast and far, it’ll do so equipped with the latest sensors and launched effects courtesy of a digital backbone that allows the platform’s capabilities to evolve with the threats.
Breaking Defense discussed the digital backbone and the Army’s Modular Open Systems Approach (MOSA) with: Galen Valentine, chief architect, FLRAA, Bell Textron; and Tanika Watson, general manager, Future Vertical Lift, GE Aerospace.
Breaking Defense: Bell’s FLRAA program is “trailblazing” for the Army’s modernization efforts, showcasing how MOSA and the digital backbone can enable rapid upgrades and integration of new technologies. First, tell us about FLRAA’s role in the Army’s Pathfinder programs.
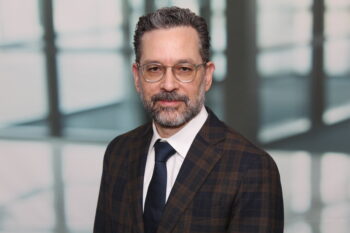
Galen Valentine is chief architect for FLRAA at Bell Textron.
Galen Valentine: A recent policy directive from the Under Secretary of the Army identified FLRAA as one of the Digital Engineering (DE) pathfinder programs. DE leverages Model Based Systems Engineering (MBSE) and digital models to provide virtual representations of the weapon system. These models define the modularity, interfaces and openness of the system, which are fundamental MOSA concepts. We have been building those models since the early stages of the FLRAA program.
Bell, as lead systems integrator, has developed and validated this unique weapon system architecture to meet the Army’s MOSA objectives using MBSE. Two of the main architectural concepts we established are the digital backbone and a common data model.
Architecturally, the digital backbone includes provisioning for space and mounting as well as power, thermal and data distribution. Designed into the architecture from the beginning, these concepts, along with the virtual system model, provide the Army a path to rapid upgrades and more organic maintenance options. As a ‘trailblazer,’ FLRAA is helping to shape the future of vertical lift platforms.
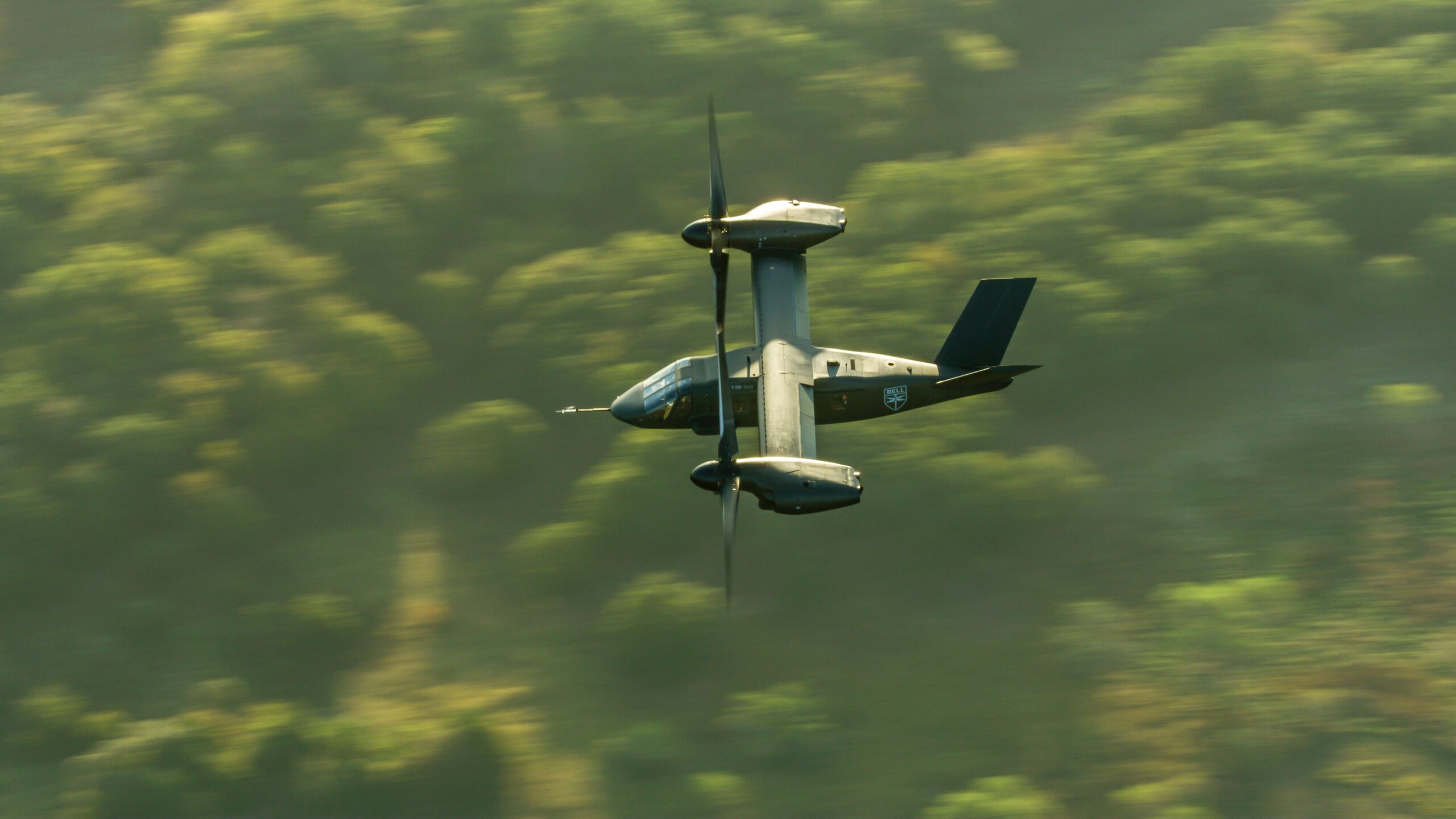
The application of MOSA and the digital backbone provides the Army with a vendor-agnostic path to make FLRAA system modifications. (Bell photo)
With FLRAA attaining Milestone B, how does the application of MOSA and the backbone become a more integral part of the aircraft’s development?
Valentine: The digital backbone is one of the primary enablers of MOSA. It is quite literally the backbone of the platform and consequently must lead the pace of development. Components cannot integrate to become a weapon system without the digital backbone.
But it’s important to remember that MOSA is not just about data or software interfaces. As a concept, the digital backbone includes, as mentioned previously, space, power and thermal distribution components, as well as network infrastructure.
We have partnered with two industry leaders, Lockheed Martin and GE Aerospace, to deliver on the vision. Lockheed Martin’s extensive pedigree and experience in software development and avionics infrastructure positions them to provide enabling software and an open computing environment.
GE’s deep experience with networks enables them to provide the configurable infrastructure and data necessary for a digital backbone. Together, our team creates the environment critical for making MOSA integral to aircraft development.

Tanika Watson is general manager for Future Vertical Lift at GE Aerospace.
Tanika Watson: Ahead of Milestone B, the FLRAA digital backbone had attained TRL6 with USG observers witnessing demonstration objectives in the Common Open Architecture Lab at Bell.
The application of MOSA and the digital backbone provides the customer with a vendor-agnostic path to make aircraft system modifications, and they can realize the benefits of MOSA designs from the outset of the Future Vertical Lift programs.
The digital backbone sometimes feels more like a concept than something concrete made out of hardware and software as mentioned earlier. Describe the elements of the digital backbone and the interfaces between systems and the backbone.
Watson: The digital backbone is composed of the physical components and the software required to make aircraft more adaptable and able to change at the speed of need.
We are delivering all of these items today: ethernet switches, nodal exchange points and the tools that enable this digital data network. We have two decades of experience in the civil market space doing exactly this type of work.
Today it is a laborious and overly long process, so one of the components of changing the current process is to adopt a new way to move data throughout the aircraft using Time Sensitive Networking, or TSN. It provides a stable, high speed, rapidly adaptable data transport ‘highway’ to meet the current and future needs.
To make this a reality, the TSN network requires physical switches to route the data to where it is needed. As a lot of the mission systems today are based on older interfaces, nodal exchange points where the data is converted from the legacy interface to TSN are required to get the data onto the digital bus.
The second component, and no less important, are the tools to make this happen. Configuring the network and putting all the data onto a single data stream is complex.
The GE Aerospace Time Sensitive Networking (TSN) Digital Backbone enables Modular Open Systems Approach (MOSA) by delivering an open, scalable, high-speed data infrastructure.
The Digital Backbone allows customers to make changes to the weapon system without going to the systems integrator, which optimizes the cost and speed of change.
GE is a key partner with Bell, providing the digital backbone technology and integration expertise to enable the MOSA approach on FLRAA, as we’ve discussed. Tell us about this relationship.
Valentine: To make the digital backbone a reality on the FLRAA aircraft, we collaborate with all our partners providing components for power, thermal, and data distribution, for example. As a key partner for data distribution and network infrastructure, we collaborate with GE to leverage their experience, tools and technology.
Watson: We work closely with Bell and the U.S. Army and will continue to collaborate on all Army platforms, legacy fleet, and unmanned air systems. For FLRAA, the collaborative approach on the digital backbone provides the Army with a vendor-agnostic path to explore and roll out new systems and capabilities when they need them.
This is a foundational effort to improve weapon system capability and affordability for the Army, so we need to work closely to ensure architectural alignment for integration of new technology.
By leveraging our experience in delivering open avionics architecture, FLRAA and the Army will realize the benefits of MOSA designs from the outset of the Future Vertical Lift programs. Providing an open, high-speed, secure, interoperable system in the digital backbone is critical to support the customer.
What were a couple differentiators in Bell’s selection of GE for the digital backbone?
Valentine: There were two primary differentiators. GE has a decades-long track record of similar technology and performance in the commercial space. This allows Bell and the Army to leverage lessons learned.
As well, GE’s participation and leadership in IEEE and SAE standards bodies demonstrated a commitment to advancing the state of the art. These standards bodies provide the industrial base a basic and consistent set of ‘rules’ for playing in the sandbox.
GE’s solution will meet the real-time time sensitive constraints of the FLRAA aircraft while allowing the Army a path for adding future capabilities.
How are Bell and GE working with others in the industry on moving MOSA and the backbone forward?
Valentine: Broadly speaking, we engage industry in conversations not only about specific enabling technologies such as TSN or general-purpose computing for example, but also how to measure success from a MOSA perspective. We participate in industry working groups, standard bodies and even MOSA summit panels.
Watson: I’ll use a statement from not so long ago from Army Maj. Gen. Walter Rugen to explain what Bell and GE are bringing to the Modular Open Systems Approach.
“The number one challenge we have with MOSA is … discipline and management. [What] allowed the enduring fleet of aircraft to wind up with different architectures [is] there was not a driving central body that said, ‘this is the architecture that you are going to go with.’ With MOSA, we have that.”
Regarding discipline, our past experience on a host of programs provides us with a unique perspective on what is required to make this work, and what it takes to keep all the actors on the same page. This is what we bring to the MOSA conversation.
MOSA does not work if suppliers are allowed to stray from the standards – keeping everyone aligned, staying on the enterprise – ‘one ring to rule them all’ architecture versus a different architecture for every platform approach. That is what Bell and GE are bringing to the table.
Our digital backbone architecture is platform agnostic. It will work on FLRAA, UH-60, AH-64, CH-47, and others. We are doing this through the use of new tools such as MBSE, digital schematics, digital environments and designs, and platform-agnostic, enterprise MOSA ways to do systems that embrace the DoD MOSA directive and make it happen. The FLRAA team is proud to be developing solutions that are readily transferable.
How does MOSA and the backbone make it possible for the Army to develop a clean-sheet design like FLRAA?
Valentine: Both concepts – MOSA and a digital backbone – more easily allow for incremental acquisition and development of a base aircraft with variants and upgrades coming later.
On the surface, traditional weapon system development does the same thing. But crucially, the intended difference is a reduction in time to field and cost by breaking vendor-lock and allowing for competition.
MOSA also enhances the ability of the Army and the OEM to identify scope that can be contracted out to suppliers offering the best technical solution with the most favorable data rights.
We are also working with our partner, Lockheed Martin, who is providing general purpose computing and Integrated Modular Avionics environments, as well as FACE-conformant software solutions to enable this.
How does MOSA and the digital backbone get FLRAA to the next phases in terms of design review for CDR and eventually first flight?
Valentine: MOSA, through modularity and well-defined open interfaces, allows internal development teams and external partners to mature component detailed designs while minimizing the impact of changes outside their scope of responsibility.
A common data model – conceptually an enabler of well-defined interfaces – defines what will be available on the digital backbone for any compliant component to consume. Well-defined interfaces allow each supplier to focus on component detailed designs.
Final thoughts?
Watson: The Digital Backbone provides the customer with a vendor-agnostic path to make aircraft system modifications, and they can realize the benefits of MOSA designs from the outset of the Future Vertical Lift programs.
Going forward, the digital backbone will change how aircraft are updated and maintained, and it ensures that our soldiers have an advantage on the battlefield.
Valentine: Fundamental for the realization of MOSA, digital engineering and the digital backbone are game changers for the Army and industry. It’s an exciting time to be a part of vertical lift and helping shape the future of weapon system acquisition and development.